For nearly 50 years, TSK CO.,LTD. has played a key role in the creation of car parts, offering expert mold manufacturing and product design.
The first question relates to the concept of monozukuri, which is well known in the Japanese manufacturing industry, particularly in the automotive industry. The kaizen philosophy or 'just-in-time' is renowned worldwide for its attention to detail. However, with increasing competition from regional rivals such as China and Korea, quality, cost, and delivery (QCD) are becoming increasingly important factors. From the perspective of a mold maker, what advantages do Japanese manufacturers have and how do they compete with such regional rivals? Injection Moulding Dies
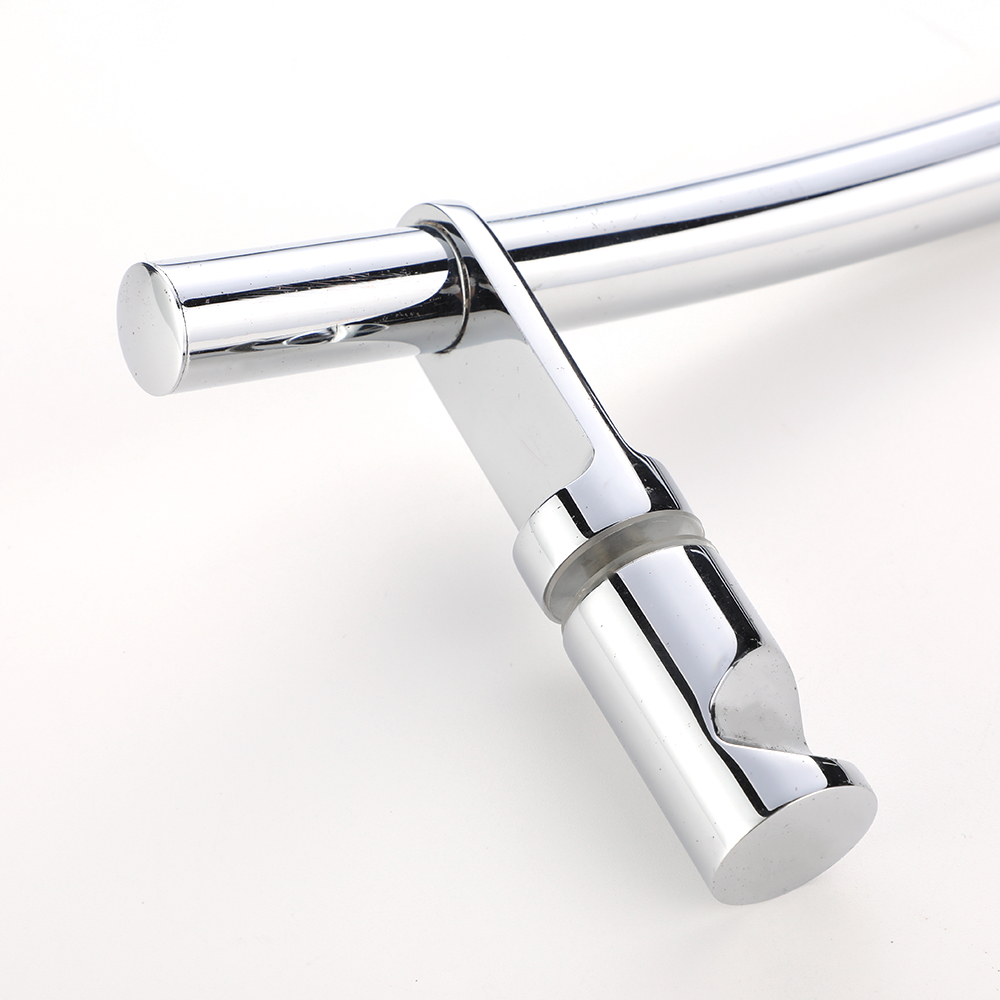
I think the advantages of manufacturing depend on the characteristics that Japanese people possess, especially in the specific business fields they have been working in. Of course, it is important to make money and increase profits, but at the same time, you want to gain the trust of your customers by honing and training all companies to become professionals in this field. This is because prioritizing customer happiness over making a profit could lead to the happiness of both the customer and the company.
Japan is an aging society, with 29% of the workforce aged 65 and over, and with a declining birthrate of only 1.3 children per couple, the population is expected to fall below 100 million by 2060. This poses a challenge in two ways: the domestic market is shrinking and it is difficult for companies to recruit talented engineers and staff. How are you facing these challenges and what steps are you taking?
Of course, Japan's shrinking population has led to a shrinking domestic market and a shortage of staff, which is a major challenge. To cope with the shrinking domestic market, we are trying to expand our market share overseas, and in 2018 we started operations in India. In the future, we are also considering expanding into African markets such as Nigeria.
To address the labor shortage, we are working on automating our manufacturing processes, and we need to consider automating CAD design and CAM data creation for mold manufacturing. Furthermore, we are also considering hiring foreign workers to compensate for the labor shortage in the country, but whether this will be successful or not remains to be seen. At the moment, our priority is automation.
Japan aims to be carbon neutral by 2050, with a 46% reduction in carbon emissions by 2030. Companies large and small are attempting to achieve more sustainable operations in the production of their end products. As a mold specialist, what are your key environmental initiatives? And what initiatives are you taking to reduce your environmental impact?
Our customers have given us a document called 'Sustainability Guidelines' and we strive to be a company that contributes to a better society. As part of our carbon-neutral initiatives, we are SBT certified until 2044, and we have created a carbon-neutral roadmap based on our activities towards carbon neutral initiatives.
Based on this initiative, we intend to increase the number of carbon-neutral tools. We also participate in the discussions and activities of the Carbon Neutral Committee and share information with members of the Supplier Association. Our customers are very accommodating.
I think one of the industries most affected by this movement toward sustainability is the automotive industry. Everyone talks about EVs, but one of the big changes is actually in the materials used inside cars. Right now, all car manufacturers, whether internal combustion engines, hybrids, or EVs, are aiming to reduce the weight of their vehicles. As a result, there is a shift towards the use of lightweight materials such as aluminum and polymers such as carbon CFRP for structural components. We want to know how these trends and changes in lightweight materials are affecting your business and your client's requirements.
You have briefly touched on the trend towards lightweight materials in the automotive industry and how this is affecting our product - weatherstrips. We understand that this trend is due to the demand for lightweight materials as well as the environmental impact associated with heavy ferrous metals such as full-scale steel.
Rubber has traditionally been used as a material for weatherstrips, but it is heavy and difficult to recycle and reuse. Resin, on the other hand, is lightweight and easy to mold, making it highly productive. However, in terms of the performance of the product itself, rubber still has several advantages.
As technology advances, resin products will become better and gradually rival rubber in performance. Are you considering a change of business to invest in resin molds?
Your question about resin molds depends on the needs of our customers.
The number of parts in next-generation vehicles will be much smaller when it comes to EVs. A typical internal combustion engine uses 30,000 parts, but in next-generation vehicles, there will be a battery, motor, and inverter, and everything else will be unnecessary. What new possibilities do you see for these next-generation vehicles? And what components can you contribute to realizing them?
The shift to EVs will continue, but this does not mean that our products will disappear. However, the shift to EVs may change the performance requirements for functional products, which we see as an opportunity for new entrants.
One question that concerns us is the concept of 'burrs', a common defect when it comes to molds. A small problem can become a big problem for the customer. I believe we have invested a lot in securing the various molds we provide to our customers. How do you ensure that the molds are free from burrs? Also, please tell us about your after-sales service to customers.
Based on the experience we have gained over the years, we can gradually change the shape and dimensions of the molds, and we can also reproduce the processing machines, so the combination of the two could lead to a variety of mold-making in this niche area.
In terms of product development, we talked about research and development. What next steps will you take to open up new possibilities in terms of product enhancement and mold design?
We receive a grant from the Japanese Government for our research and development activities. We have used that grant to spend most of our investment on processing technology. As I mentioned earlier, the accuracy required for texture processing is increasing day by day. To cope with this, we are trying to innovate our technology and equipment.
In the past, customers used to demand one micron. But now they demand nanometres, three orders of magnitude smaller. It is very difficult to process that small size all at once. Gradually, we are trying to update our technology and processes to meet customer requirements as a process.
However, if we can achieve the machining accuracy and quality of the molds that our customers require, we will soon be able to add value to our products and meet the quality requirements of our customers in the future. If we can achieve that, it would be very good and very important. That is why we have already started investing.
Apart from investment, I am also interested in the role of partnerships and open innovation to enhance technology. When I interviewed Mino, they were in Mexico. They make die-cast aluminum ECU cases. They told us that they are working with local partners in Europe, Mexico, and here in Asia to enhance their technology. Can you tell us a bit about your company and co-creation? Are you looking for partners, especially abroad, who can help you enhance this technology?
Based on the partnerships we have experienced, we have two types of partnerships. Rather than looking for mold makers abroad, we already have offices and locations in five different parts of the world. However, there are Japanese mold makers, resin manufacturers, and molding companies in Japan, including interior and exterior and safety systems. Those companies have not yet expanded overseas.
By partnering with us, those safety system manufacturers and mold makers that have not yet expanded overseas can use our factories to provide products such as interior and exterior systems to their customers. Such partnerships have already started.
Another partnership is about partnerships with molding manufacturers. Toyota has a lot of bases, so they don't have to work closely with us, but we have other customers. I cannot give you specific company names, but in the future, we would like to go to India, for example, and supply molded products to those overseas markets.
If we can work together in partnership with our company, we can also produce and sell molds and molded products. That is what we would like to do with them in the future through partnerships.
If you look at the world map, we are very strategically located. Indonesia, China, and Mexico. Which regions and markets do you see as having the most potential in the future?
Of course, India. Also, Mexico is a big market that is very close to the US and North American markets. As for the Chinese market, it is very complicated and we are worried about it. This is one way of thinking.
We have just lived through two years of a coronavirus pandemic. There have been a lot of supply chain disruptions and logistical disruptions because of China's zero-combined policy. In Shanghai, there has been a blockade of the Toyota plant. It is a very big problem. As a result, we see that large companies like Tier One and OEMs like Toyota are shortening their supply chains and localizing their production. On top of that, Japan has excellent automation technology and the rate of the Japanese yen against the US dollar is quite low, so it is much cheaper to produce in Japan. In many interviews conducted in the last month or two, many presidents said that they think manufacturing will return to Japan. For this reason, production will return to Japan. Do you think so? Do you think this will happen in the future?
I don't think so, because of the high shipping costs. If you have customers in Thailand, if you have customers in India, etc., you have to deal with local production. Also, if the Japanese Government focuses only on exporting products from Japan to other countries, this could lead to trade friction, and localization is also necessary, as localization could favor certain countries in the world. In the end, it could lead to trade friction, which is what we would like to do if we could, but maybe we can't.
Imagine you came back for another interview in 10 years: what goals and dreams would you like to have achieved and communicated in the interview in 10 years?
I would be very happy to talk about the molding process and product details. We have already achieved single nanofabricated weatherstrips as well as high-precision components.
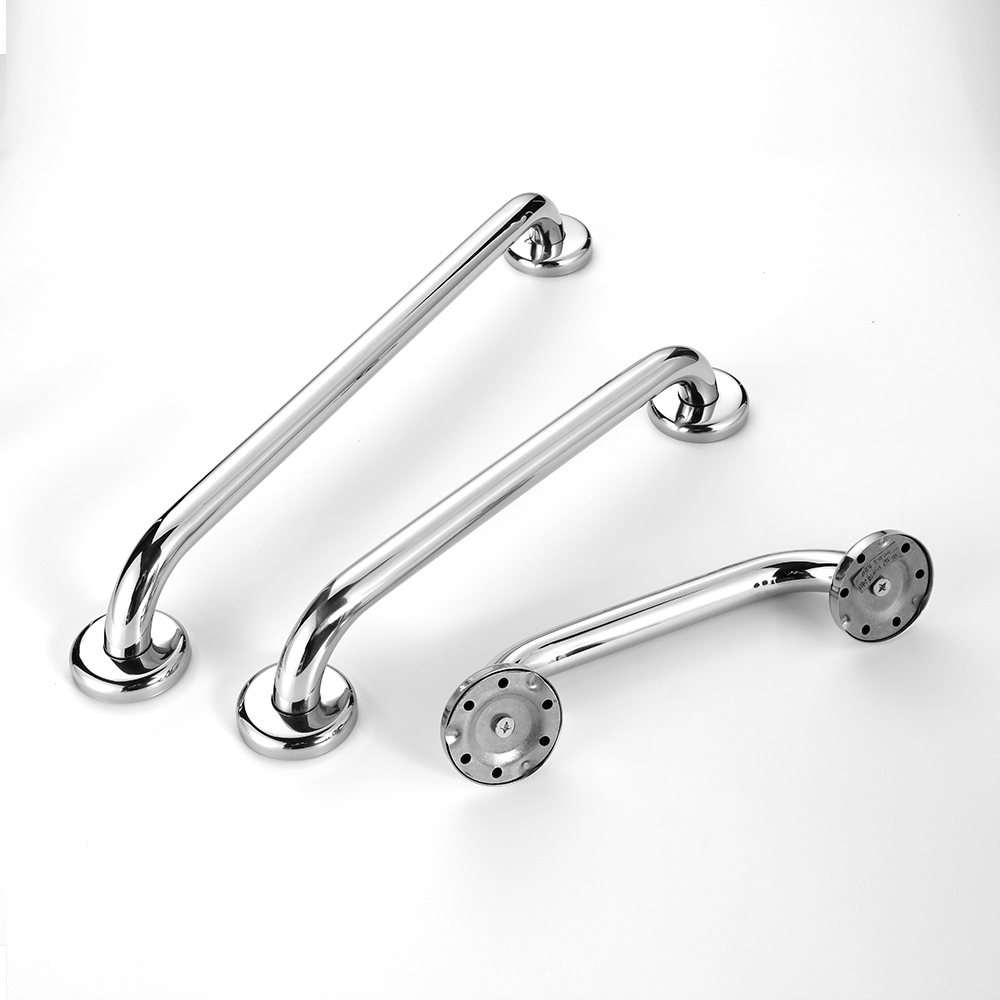
Plastic Auto Body Parts The Worldfolio provides business, industrial and financial news about global economies, with a focus on understanding them from within.