is part of the Informa Markets Division of Informa PLC
This site is operated by a business or businesses owned by Informa PLC and all copyright resides with them. Informa PLC's registered office is 5 Howick Place, London SW1P 1WG. Registered in England and Wales. Number 8860726. Car Emergency Kit Window Breaker
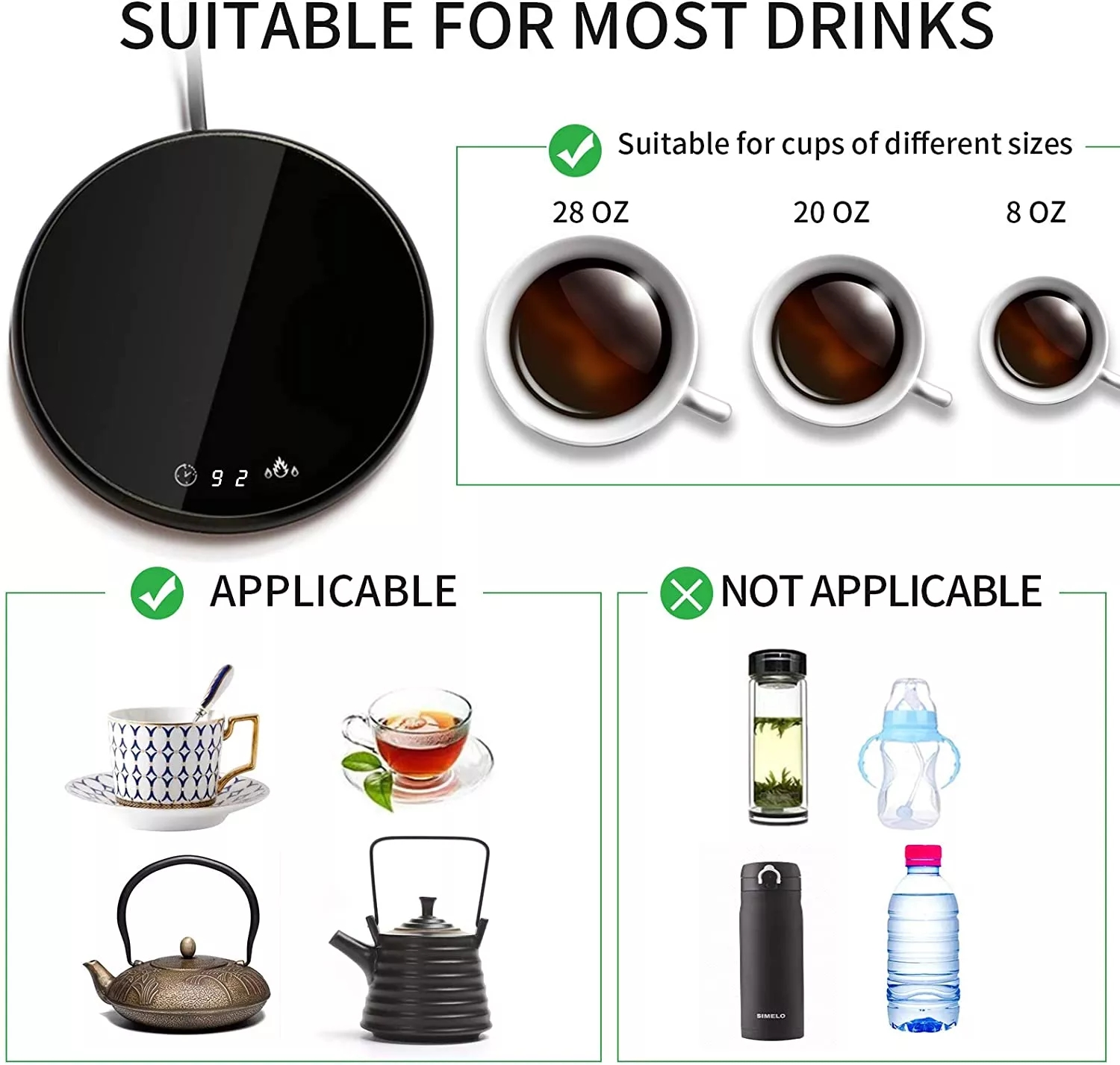
Whether building a full plant or just adding a new cell to an existing production system, great care must be put into preparation prior to the actual installation of equipment. This article will outline the steps required to ensure the success of your equipment installation and process development.
Developing the production layout is the first step to review. A cell should be planned according to equipment size and height while maximizing space usage. Proper planning also should take into consideration small and large maintenance procedures. A mold change system should be developed to allow quick mold changes. If multiple mold changes will be performed, a hoist might best serve your needs. If few molds will be changed out, perhaps a shuttle system will suffice. Even if a mold is married to a press, planning needs to include mold service needs. In addition, a flow-through production system should be developed when possible. Machine production flows to assembly, which flows to warehousing (if applicable), and then to dock. Eliminating waste-of-motion from your production system helps to streamline efficiencies.
Press and robotics planning are also key to the success of a production system. When adding a new machine or robot, review the OEM’s participation, technical support, and parts availability. Also review the machine controller. How robust is the controller and is it operator friendly? Will your operation be best served by a specialty screw based on the use of a primary material? Will mold thickness and open daylight settings require press modification? Can hot runner and water setpoints be reviewed on the controller? Is the robotic system you are planning to deploy robust enough to complement the automation you are planning to use? Is the robot controller user-friendly? It is also important to have personnel familiar with the controllers of both the machine and robot. If you are installing used equipment, it is important to note that as equipment ages, the costs of unplanned maintenance increase. This can affect scheduling; in some cases, lead times on replacement parts can be long.
It is important to validate that the air compressor is large enough to run the press, robot, material loading system, and any other pneumatic functions needed for your production system. Failure to do so limits your production capabilities. Equipment might perform poorly in some cases, leading to poor production numbers and even equipment damage.
In most cases, the loading system should be placed in a central location to reduce material change times. Hopper throughput should be calculated to verify that material being dried spend an adequate amount of time in the hopper. Make sure there are enough pumps available to operate your loading system.
It is absolutely crucial that your plumbing system provide adequate pressure, turbulent flow, and cooling required by your operation. Flow rates require a minimum of 10 gallons per minute (GPM), but preferably 15 to 24+ GPM. Failing to do this can affect temperature control units and even lead to mold damage. In addition, avoid using PVC piping, which can be damaged by forklifts. Planning should include installation and monitoring of GPM to and from the mold, as well as overall system pressure.
If tooling is being built, ensure that your tooling company is credible and familiar with the application you are developing. Molds built overseas can be cost effective, but only if mold design is being overseen by an experienced mold designer/tool maker. Cheaper is not always better. If your company is taking in outsourced molds, verify that you have the proper equipment to mold parts off these molds effectively. At a minimum, an onsite tool room should perform preventive maintenance and small service and repair. When choosing a tool shop, make sure your tool maker is familiar with the size and types of molds requiring service. Although the location of the tool shop is preferably within three hours of your operation, tool shop capabilities, efficiencies, and performance are equally critical considerations.
Developing a cell or plant is a large undertaking that requires meticulous planning, observation, and installation. Rushing the engineering process leads to poor efficiencies and even failure of the manufacturing system. Take the time to properly develop the production system to ensure its success and your prosperity.
Got a problem with this, that, or the other thing? You might find answers in some previous "Troubleshooter" columns:
How to Identify and Correct Shear-Related Splay Defects
The Role of Moisture in Injection Molding Splay Defects
Preventing Flash in Injection Molded Parts
How to Prevent Common Failure Modes in Injection Molding
Building a Validated Plastic Injection Molding Process
Fixing Color Defects in Injection Molded Parts
Key Steps for a Stable Injection Molding Process
Garrett MacKenzie is the owner/editor of plastic411.com and a consultant/trainer in plastic injection molding. He has provided process-engineering expertise to many top companies, including Glock, Honda, Johnson Controls, and Rubbermaid. MacKenzie also owns Plastic411 Services, which provides maintenance and training support to Yanfeng Automotive Interior Systems, IAC, Flex-N-Gate, and other top automotive suppliers. He was inducted into the Plastic Pioneers Association (PPA) in 2019, where he serves on the Education Committee evaluating applications from college students seeking PPA scholarships. You can reach him via e-mail at [email protected] .
More information about text formats

Complex Injection Molding Check out our coverage of mind-blowing new plastics applications and more.