Do you want to save interesting articles to your personal bookmarks? Please register here:
Already have an account? Please sign in here: Login Carbide Mining Bits

Researchers are now further exploiting the potential of additive manufacturing to produce tungsten carbide-cobalt tool electrodes for electrical discharge machining with an eye on industrial applications.
The increasing complexity of components and the continuous advances in tool and mould making require constant developments in manufacturing processes such as electrical discharge machining (EDM). This is done, for example, through the development of new types of process chains for the production of complex tool electrodes. Additive manufacturing (AM) enables the production of complex tool electrode geometries with internal flushing channels for EDM processes with few restrictions in terms of design. Tungsten carbide-cobalt (WC-Co) represents a suitable material for EDM tool electrodes that has high thermal and mechanical stability and can also be processed additively. This article shows the first results of studies on the use of additively manufactured WC-Co tool electrodes in die-sinking EDM. The Institute for Machine Tools and Factory Management IWF at the Technical University of Berlin and the Fraunhofer Institute for Production Systems and Design Technology IPK are involved.
Dr.-Ing. M. Polte, Senior Engineer, IWF, Technical University of Berlin; R. Hörl, M. Sc., Research Assistant, IFW, Technical University of Berlin; R. Bolz, M. Sc., Research Associate, IWF, Technical University of Berlin; Th. Braun, M. Sc., Research Associate, IWF, Technical University of Berlin; R. J. Neuschäfer, B. Sc., Assistant Scientist, IMF, Technical University of Berlin
Previous studies ([1], [2] and [3]) on the AM process Laser Powder Bed Fusion of WC-Co material demonstrated an influence of the energy density Ev on the cobalt content CCo of the manufactured samples. In the present study, tool electrodes were manufactured by AM process with preheated processing chamber and WC-Co 83/17 (as powder material) and these were analysed with regard to their influence on the EDM process.
By varying the energy density in a range 300 J/mm3 ≤ Ev ≤ 900 J/mm3 in four steps, the cobalt content CCo and the associated material properties of the components such as relative density ρrel and electrical conductivity κ were influenced. For each energy density Ev, two samples were fabricated and analysed accordingly. In order to evaluate the suitability for die-sinking EDM, further tests were carried out with additively manufactured tool electrodes. The samples were evaluated by determining the removal rate VW and the relative tool wear ϑrel for the respective EDM tests.
In addition, numerical simulations were performed to investigate the internal flushing of the tool electrodes to improve the material removal behaviour. In order to determine the maximum flow velocity v and the volume flow V in the working gap, three different flushing channel geometries were investigated. The tests were carried out for different flushing channel cross-sectional areas in a range of 0.196 mm2 < Ac < 0.785 mm2 and different inlet pressures in a range of 2 bar ≤ pc ≤ 40 bar.
The results showed that for AM processes with an energy density of Ev = 500 J/mm3 the highest relative density could be achieved at ρrel = 87 percent. Indeed, a sufficiently high relative density is required for the mechanical strength σm of the tool electrodes for use in die-sinking EDM to withstand high flushing pressures pS The samples, which were produced with an energy density of Ev = 900 J/mm3, were not suitable for the spark erosive sinking process due to their low relative density ρrel.
The measurement of the cobalt content CCo showed the highest values at energy densities of Ev = 300 J/mm3. Due to the measurement setup, an offset for the values of the cobalt content was shown. For cobalt contents of CCo > 17 percent, it can also be concluded that no cobalt was vaporised during the AM process. A high cobalt content can possibly increase the electrical conductivity κ of the tool electrode, which has a positive effect on the EDM process. This could be confirmed in the die-sinking EDM tests. There, the removal rate was highest with V̇w = 5.53 mm3/min at an energy density of Ev = 300 J/mm3.
The analysis of the relative tool wear ϑrel showed that the samples produced with an energy density of Ev = 700 J/mm3 were subject to the highest relative tool wear, which was 10.2 percent. This can be attributed to porous structures created by the additive manufacturing process. Additively manufactured samples with an energy density of Ev = 300 J/mm3 and Ev = 500 J/mm3 showed a slightly lower wear with ϑrel = 9.6 percent. It follows that energy densities between 300 and 500 J/mm3 are best suited for additive manufacturing of EDM electrodes. This range will therefore be investigated further in the future.
By clicking on „Subscribe to Newsletter“ I agree to the processing and use of my data according to the consent form (please expand for details) and accept the Terms of Use. For more information, please see our Privacy Policy.
Naturally, we always handle your personal data responsibly. Any personal data we receive from you is processed in accordance with applicable data protection legislation. For detailed information please see our privacy policy.
I hereby consent to Vogel Communications Group GmbH & Co. KG, Max-Planckstr. 7-9, 97082 Würzburg including any affiliated companies according to §§ 15 et seq. AktG (hereafter: Vogel Communications Group) using my e-mail address to send editorial newsletters. A list of all affiliated companies can be found here
Newsletter content may include all products and services of any companies mentioned above, including for example specialist journals and books, events and fairs as well as event-related products and services, print and digital media offers and services such as additional (editorial) newsletters, raffles, lead campaigns, market research both online and offline, specialist webportals and e-learning offers. In case my personal telephone number has also been collected, it may be used for offers of aforementioned products, for services of the companies mentioned above, and market research purposes.
In case I access protected data on Internet portals of Vogel Communications Group including any affiliated companies according to §§ 15 et seq. AktG, I need to provide further data in order to register for the access to such content. In return for this free access to editorial content, my data may be used in accordance with this consent for the purposes stated here.
I understand that I can revoke my consent at will. My revocation does not change the lawfulness of data processing that was conducted based on my consent leading up to my revocation. One option to declare my revocation is to use the contact form found at https://support.vogel.de. In case I no longer wish to receive certain newsletters, I have subscribed to, I can also click on the unsubscribe link included at the end of a newsletter. Further information regarding my right of revocation and the implementation of it as well as the consequences of my revocation can be found in the data protection declaration, section editorial newsletter.
In addition, a numerical model was developed for the investigation of the internal flushing channels of the tool electrodes in order to be able to carry out the studies in a time- and resource-saving manner. Round, rectangular and cloverleaf-shaped flushing channel cross-sections for different input pressures pin and flushing channel cross-sectional areas Ac were investigated. When analysing the flow velocity v in the lateral working gap, a cloverleaf-shaped geometry showed the highest flow velocities for each inlet pressure pin and each flushing channel cross-sectional area.
Further investigations were carried out in the area of the frontal working gap. This is where most spark discharges occur during the EDM process and where disturbing particle deposits occur. For this reason, effective flushing in this area is necessary for a stable EDM process.
The analysis of the flow velocity v and the eddy viscosity νt showed that a rectangular geometry as flushing channel cross-section leads to the highest values for both parameters. A visual representation of steel particles in the frontal working gap during rinsing confirmed that the higher flow velocity and eddy viscosity in the rinsing channel of the rectangular geometry leads to a significantly increased transport of ablation particles. It is likely that a flushing channel geometry that leads to increased turbulence in the working gap ensures a better overall flushing effect during the EDM process.
In summary, the rectangular channel structure is best suited for internal flushing, even though it has lower flow velocities vc in the lateral working gap than the comparison geometries. With the results obtained, suitable parameters were found for the additive manufacturing of tool electrodes made of WC-Co for use in EDM processes. In the future, the potential of more complex internal flushing channels can thus be exploited on the basis of these findings. The results of the numerical modelling already showed positive tendencies to improve the flushing of the working gap.
[1] Uhlmann E, Bergmann A, Bolz R, Gridin W. Application of Additive Manufactured Tungsten Carbide Tool Electrodes in EDM. Procedia CIRP. 2018; 68: 86 – 90.
[2] Uhlmann E, Polte J, Bolz R, Yabroudi S, Streckenbach J, Bergmann A. Application of additive manufactured tungsten carbide-cobalt electrodes with interior flushing channels in S-EDM. Procedia CIRP. 2020, 95: 460 – 465.
[3] Polte J, Neuwald T, Gordei A, Kersting R, Uhlmann E. Effects on part density for a highly productive manufacturing of WC-Co via Laser Powder Bed Fusion. Proceedings euspen, International Conference & Exhibition. 2021, 21.
* All authors conduct research at the Institute for Machine Tools and Factory Management IWF at the Technical University of Berlin. Eckart Uhlmann and Mitchel Polte also work at the Fraunhofer IPK in Berlin.
Micromilling on 384 component sections to an accuracy of 5 micrometres
Unlocking precision and efficiency with EDM, measuring and automation
Imprint Cookie-Manager About Media Privacy General Terms and Conditions Help
Copyright © 2024 Vogel Communications Group
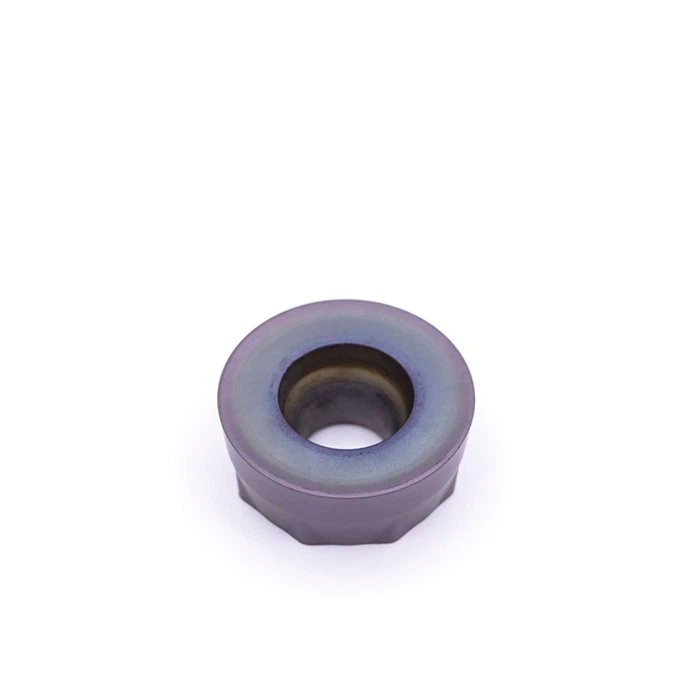
Tungsten Carbide Saw Tips This portal is a brand of Vogel Communications Group. You will find our complete range of products and services on www.vogel.com