We use cookies to enhance your experience. By continuing to browse this site you agree to our use of cookies. More info.
On-line analyzers are of growing importance for process monitoring, optimization, and control of numerous large-scale applications across the refining, petrochemical, power generation, metals, and biotechnology industries. In Situ Gas Analyzer
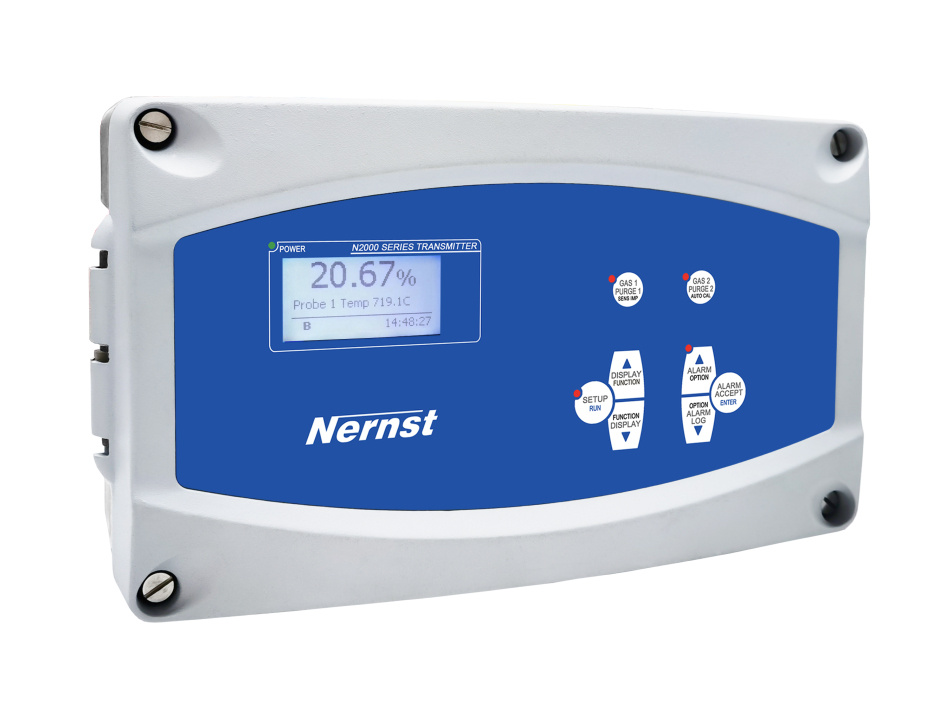
Instruments must produce rapid, accurate, and thorough real-time gas measurements in industrial processes to enable operational conditions to be checked regularly and quickly corrected if they stray from the required parameters.1
Additionally, reliable on-line analytical data is crucial for the efficient and safe operation of production plants and for fulfilling the strict legislative requirements that are progressively being set by health and safety, energy conservation, and emissions control protocols.
Selecting the appropriate system and technology is vital, with aspects including footprint, long-term cost, sample time, ease of maintenance, precision, and sensitivity needing to be considered.
Traditionally, on-line monitoring has been reliant on gas chromatography (GC), and, despite technicians being familiar and confident with this robust industry standard, mass spectrometry (MS) is becoming the frontrunner for such applications.
This article compares MS and GC analyzers for on-line monitoring of industrial processes and outlines the reasons why plants should upgrade to scanning magnetic sector MS instruments for quicker, more accurate, and more comprehensive gas analysis with improved long-term affordability.
On-line analyzers carry out continuous measurements of gas streams to enhance control, supply product details, and identify impurities.
Industrial plants need reliable gas stream data to enable the optimization of their processes, adjust the reaction mixture for maximization of product yields, enhance the finished product quality, and guarantee safety within the production plant.
Numerous large-scale operations demand carefully balanced conditions and quick decisions on any parameter changes within a process since delays of just one minute can lead to huge losses.
GC is the most common technique for on-line monitoring of gases within production lines, largely because of its low cost per instrument, ease of automation, familiarity with the method, as well as the ability to simultaneously measure numerous components.
GC involves the separation and analysis of hundreds of individual species, even in complex mixtures, and measures the composition both quantitively and qualitatively.
Gaseous samples are distributed between a stationary and mobile phase, while molecules are carried by a chemically inert gas through a heated column. Results are available in a few minutes with very low detection limits and high precision.
Although GC is a popular method, it does have weaknesses. Firstly, a process gas chromatograph provides results at intervals of minutes. This limits the technique’s suitability for automatic control and on-line analysis where a delay between sampling and analytical time does not enable immediate reaction correction.2
This is mainly due to the time-consuming chromatographic separation of components as the sample moves through the column.3,4 Speed is highly advantageous for on-line protocols, particularly as plants will frequently assess two or three sequential data points before any action is taken to change a process.
With GC, several instruments or columns may be used in tandem to decrease the measurement interval and prevent slow analysis times. Plants tend to install an array of GC units to attain continuous monitoring of multiple components, with the longer cycle time of GC meaning that it is frequently used on a single stream basis.
However, this leads to additional costs and constraints. Large configurations of GC units — with intensive maintenance schedules to protect against retention time drift — are usually housed outdoors to save valuable laboratory space, demanding large, costly, purpose-built shelters.
There are also further costs for replacement columns, and calibration and carrier gases.
MS is a powerful and sensitive method that delivers a highly specific and versatile solution for analyzing and controlling industrial production lines with significant advantages in comparison to GC.
Mass spectrometers characterize numerous aspects of a chemical reaction, such as the creation of products and impurities and the consumption of reactants. They effectively ionize neutral sample gas molecules to charged particle components which are subsequently separated by their molecular weight.
Mass spectrometry’s analytical power mostly comes from its speed, dynamic range, sensitivity, and multiplexing and multicomponent analysis capability.5
MS detectors enable the establishment of compounds of the most diverse elemental composition while simultaneously determining the structural features of components.4
Despite process MS analyzers being relatively more complex and initially more costly to implement than GC, they provide unmatched precision (typically several orders of magnitude higher) and speed as well as more long-term cost-effectiveness.3
An MS instrument based on scanning magnetic sector technology where charged particles are separated in a variable magnetic field is displayed in Figure 1. These deliver flat-topped peak profiles that tolerate mass scale drift with no impact on measurement results.
This leads to reduced maintenance times, high stability, and maximum availability for plant productivity.5
Figure 1. Schematic of a magnetic sector process mass spectrometer. Image Credit: Thermo Fisher Scientific – Environmental and Process Monitoring Instruments
These analyzers are able to measure very small concentrations immediately adjacent to high concentrations as a result of the clean baseline between peaks, offering excellent reproducibility and linearity.
This flexible and powerful technology is perfect for exceptionally stable and rapid gas analyses with unparalleled accuracy, precision, resistance to contamination, and lengthy intervals between recalibration.
Process MS analyzers can conduct direct analysis on numerous sample streams, with a single instrument replacing multiple GC units. This leads to a lower total footprint and overall capital costs.
Instruments that utilize scanning magnetic sector MS, e.g., the compact and rugged Thermo Scientific™ Prima PRO (as shown in Figure 2), are well suited for the challenging applications in process monitoring.
Figure 2. Prima PRO Process Mass Spectrometer. Image Credit: Thermo Fisher Scientific – Environmental and Process Monitoring Instruments
The Prima PRO magnet is laminated to enable high-speed scanning for rapid analysis while preserving excellent stability. It is supplied with the unique rapid multi-stream sampler (RMS) to deliver fast, reliable sample selection from up to 64 streams, as displayed in Figure 3.
Figure 3. The Prima PRO’s 32-port rapid multi-stream sampler (RMS). Image Credit: Thermo Fisher Scientific – Environmental and Process Monitoring Instruments
It can measure gas component concentrations with precision in the range of 10 parts per million (ppm) to 100% with one Faraday detector. The analyzer uses Thermo Scientific GasWorks Software to guide operations and offer a secure and stable platform for process analytics (see Figure 4).
Figure 4. GasWorks Software sample display. Image Credit: Thermo Fisher Scientific – Environmental and Process Monitoring Instruments
Thermo Fisher Scientific also provides service and support options with promised response rates to guarantee timely instrument optimization.
Table 1. Comparing the features of a standard process GC with the Prima PRO process MS. Source: Thermo Fisher Scientific – Environmental and Process Monitoring Instruments
The Prima PRO conducts analysis in 10 to 20 seconds if the analyzer inlet remains on a single sample stream, compared to the 3 to 15 minutes often observed on standard process GC analyzers, with actual analysis time dependent on the complexity of the target gas.
A single Prima PRO can measure many sample points with very quick cycle times by plumbing multiple streams into the same instrument’s RMS, reading data points on these sample streams every 30 seconds, including the 10 seconds required to flush out the previous gas.
Analysis of fuel gas components is approximately five times more precise on the Prima PRO than when using a standard process GC.
Performance evaluations have demonstrated that the Prima PRO provides significantly better linearity than a thermal conductivity detector fitted to a gas chromatograph when conducting analysis of complex gas mixtures (see Figure 5).6,7
Figure 5. Prima PRO linearity data generated by EffecTech. Image Credit: Thermo Fisher Scientific – Environmental and Process Monitoring Instruments
The Prima Pro’s rugged and fault-tolerant design results in exceptional availability greater than 99.7 %, reaching 100 % with redundant installation.
This reliability substantially decreases the maintenance requirements of the Prima PRO, which further reduces operation costs, freeing up time for a maintenance manager to perform other tasks, especially compared with the maintenance required by multiple legacy GC units.
The Prima PRO’s typical calibration interval is between one month and 90 days and usually occurs automatically.
A standard process GC might demand, for example, a six-week preventative maintenance schedule for valves and quarterly maintenance on other instrument parts, with common applications needing daily calibrations.
Although the initial expense for the Prima PRO (approximately US $175k) is higher than that for a standard process GC (approximately US $50 to 75k), a single system executes the job of multiple GC units, reducing the total cost of ownership, shelter size, and maintenance.
Unlike a process GC analyzer, the Prima PRO does not require the separation of the sample using a column, preventing consumables costs on replacement columns, in addition to calibration and carrier gases.
Table 2 details a 10-year customer case study that analyzed the total cost difference from replacing two legacy process GCs with one Prima PRO for flare gas monitoring.
The Prima PRO delivers rapid, accurate, and multicomponent analysis for a plant stack, making it ideal for this demanding application that involves the analysis of highly complex gas streams.
At the end of the ten years, total operating costs were decreased by almost half, mostly due to lower utility costs and substantially reduced consumables expenses.
Table 2. Customer case study cost analysis over 10 years comparing one process MS (Prima PRO) with two legacy process GCs. Source: Thermo Fisher Scientific – Environmental and Process Monitoring Instruments
Manufacturing process demands and associated legislative requirements have resulted in a need for fast, reliable, and accurate process analyzers at affordable costs.
The choice of on-line analyzer has predominantly been steered by familiarity, but it is evident that the highly versatile magnetic sector MS can deliver faster analysis at greater levels of precision — with fewer analyzers — and these systems are growing in popularity as a result.
The Thermo Scientific Prima PRO is a perfect example of this; it is optimally suited to industrial process monitoring, and, despite MS being relatively more complicated and costly to implement, a single instrument can conduct the work of multiple GC units to decrease sample time, simplify maintenance, and reduce overall costs.
The Prima PRO MS provides rapid, precise, and comprehensive on-line gas composition analytics that is unparalleled, in addition to highly favorable flexibility compared to a standard process GC, guaranteeing a strong return on investment.
It is constructed to satisfy the application-specific needs of today. It is already the system of choice in plants and refineries worldwide to monitor emissions and optimize a variety of production processes, and it is set to be the industry standard in the future.
This information has been sourced, reviewed and adapted from materials provided by Thermo Fisher Scientific – Environmental and Process Monitoring Instruments.
For more information on this source, please visit Thermo Fisher Scientific – Environmental and Process Monitoring Instruments.
Please use one of the following formats to cite this article in your essay, paper or report:
Thermo Fisher Scientific – Environmental and Process Monitoring Instruments. (2023, May 26). On-Line Gas Analysis through On-line Gas Chromatography or Mass Spectrometry. AZoM. Retrieved on October 25, 2023 from https://www.azom.com/article.aspx?ArticleID=22663.
Thermo Fisher Scientific – Environmental and Process Monitoring Instruments. "On-Line Gas Analysis through On-line Gas Chromatography or Mass Spectrometry". AZoM. 25 October 2023. <https://www.azom.com/article.aspx?ArticleID=22663>.
Thermo Fisher Scientific – Environmental and Process Monitoring Instruments. "On-Line Gas Analysis through On-line Gas Chromatography or Mass Spectrometry". AZoM. https://www.azom.com/article.aspx?ArticleID=22663. (accessed October 25, 2023).
Thermo Fisher Scientific – Environmental and Process Monitoring Instruments. 2023. On-Line Gas Analysis through On-line Gas Chromatography or Mass Spectrometry. AZoM, viewed 25 October 2023, https://www.azom.com/article.aspx?ArticleID=22663.
Do you have a question you'd like to ask regarding this article?
AZoM.com - An AZoNetwork Site
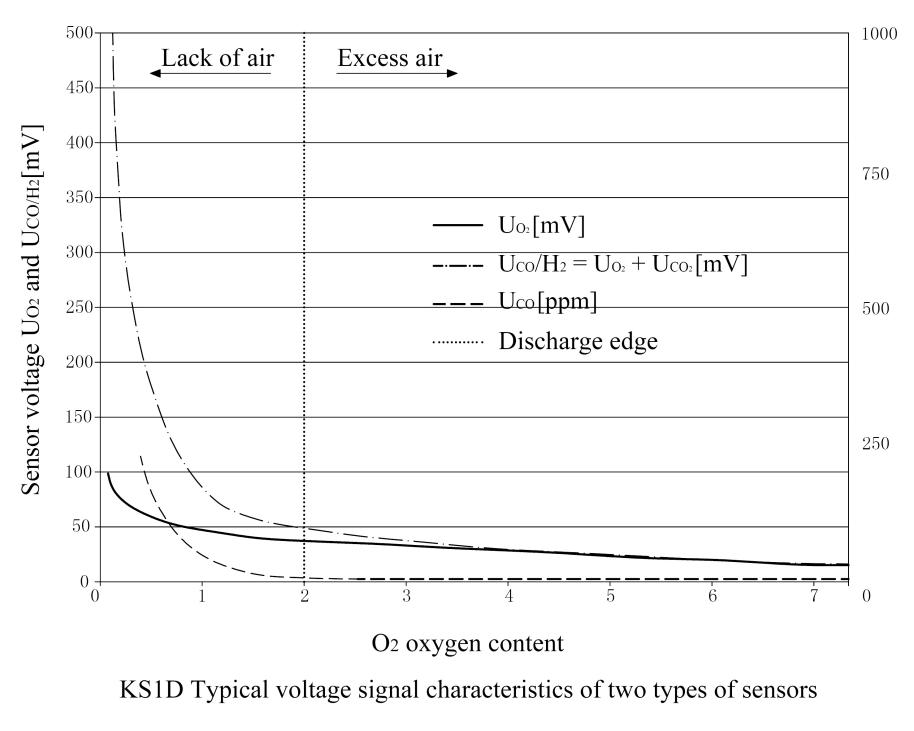
Zirconia Oxygen Probe Owned and operated by AZoNetwork, © 2000-2023