Exhibitors at ITMA 2023 showcased the latest weaving technologies, which showed a continued commitment to sustainable production and digitization.
By Dr. Abdel-Fatah M. Seyam, Technical Editor Minute Repeater Movement Factory
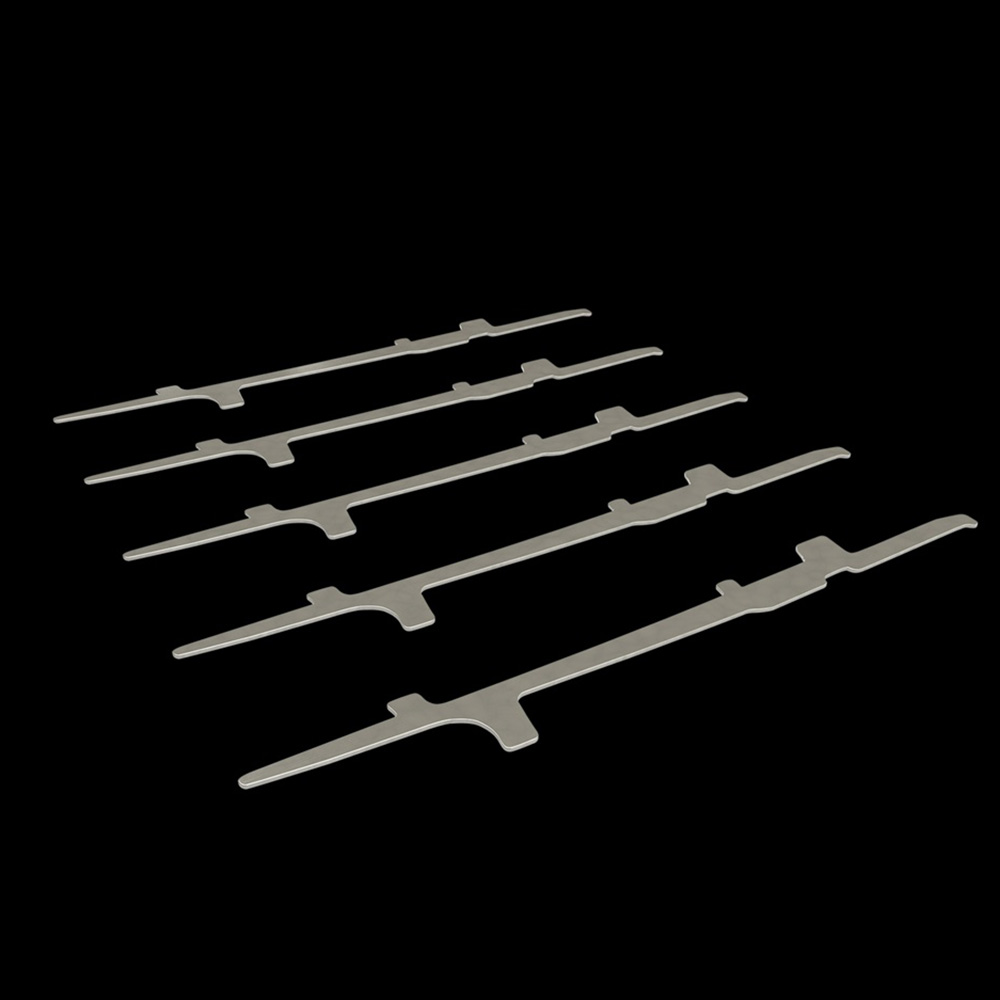
R esponding to environmental concerns and demand from consumers, textile machinery manufacturers are developing technologies to address sustainability in terms of reducing manufacturing waste, saving in energy and water consumption, and producing yarns and fabrics from recycled and biobased fibers. The technologies exhibited at ITMA 2023 revealed the continued commitment of the machine manufacturers, which started at the previous ITMA show, to focus on sustainability and digitization that light the road to Industry 4.0. It should be noted that sustainability and digitization are highly interrelated.
This paper covers some notable innovations in weaving technologies exhibited at ITMA 2023. As seen at previous shows, machine manufacturers continue to develop and improve their equipment to form diversified products for apparel, home and technical textiles markets.
Several exhibitors demonstrated weaving yarns from recycled fibers at high-speed. At the previous ITMA show, machine manufacturers marketed their technologies as Industry 4.0 ready, which has continued at this ITMA with more development in digitization. The last three decades have witnessed a dramatic increase in automation, control, monitoring of production and performance, and data storage in super computers and cloud and communication to access the data using electronic devices.
Sample preparation technologies were developed for rapid prototyping. Prior to the development of sample technologies, weavers used production machines to develop prototypes, which led to significant loss of production and raw materials.
Sample warpers were advanced to not only produce prototypes, but also small and medium orders for diversified line of production. Today, because of their numerous advantages, sample warpers are used not only by weavers, but also by universities and research institutions.
At ITMA 2023, Germany-based KARL MAYER Group exhibited a compact version of the automatic sample warping machine MULTIMATIC® 32 Compact with creel capacity 32 wound packages for short and medium length warps. The machine was producing an intricate striped warp. The MULTIMATIC 32 Compact is characterized by its high production, interactive multiflexible movable creel, fast pattern changes and short setup times. The increase in productivity is achieved by eliminating the stop for leasing and sizing separation.
The company offers LINKMATIC® automatic systems to increase the productivity of indigo and sizing machines by up to 30 percent. After completing a warp beam set, the system is used for tying-in the warp yarns from the new warp beam set to the set just completed.
LINK-MATIC is designed to be managed by only one operator and reduce material waste. Karl Mayer’s machines, including warp preparation systems, are networked via cloud for efficient access to machine data and remote service.
Production and quality management reports stored in the cloud can be accessed by electronic devices such as mobiles and laptop or desktop computers. Its software offering KM.ON offers customers individual solutions that include production data analysis tools for flexibility and efficiency.
Belgium-based VANDEWIELE NV again showed its Smart Creel that was introduced at the previous show. The creel is very compact compared to a traditional creel because the large wound packages are replaced with much smaller cells/holders arranged in rows and columns. Robots are used to wind the pile yarns from large wound packages with the exact length needed per weaving pattern.
Germany-based Groz-Beckert KG showed its KnotMaster as well as the WarpMasterPlus drawing-in machine that were on display at past ITMAs. The WarpMasterPlus is equipped with a computer system with swivel monitor or a touch screen user-interface with operator guided visualization that provides instructions on operation and troubleshooting via videos. Two monitors are available as an option to facilitate operator monitoring because the machine is long at between 2.4 and 4 meters. The machine consists of the drawing-in needle, drop wires, heddle wires, reed, and a single yarn from a wound package and their associated modular mechanisms. The yarn is fed to the machine by a feeder that is similar to a weft yarn feeder in weaving. The heddle wires and drop wires, which are loaded by an operator, are fed automatically to the drawing-in zone. The single yarn is fed to the drawing-in needle that threads the yarn through a drop wire eye, a heddle wire eye, and a reed dent. Then the yarn is cut, and the procedure is repeated at up to 150 times/min depending on the yarn type. After the drawing-in is completed, the drop wires are transferred to drop wire bars and the heddle wires to harnesses. The harnesses, drop wire bars, and reed are moved on a trolley to a storage area. When a weaver’s beam is ready, the drawn-in warp from a single yarn is knotted to the corresponding warp yarns using a tying-in machine. Then warp beam, read, harnesses, drop wires bars are moved to the weaving area to supply a new warp to a weaving machine according to production planning. Due to the absence of the weaver’s beam because of using a single yarn, the drawing-in machine occupies less space. However, space is required at the next step for the weaver’s beam and tying-in process post drawing-in. While the drawing-in process is faster and setup time is shorter as a result of the simplicity of drawing from a single yarn, additional time is needed for knotting the weaver’s beam yarns to the drawn-in yarns.
Switzerland-based Stäubli showed its tying-in machine TIEPRO that was unveiled at ITMA 2019, while revealing more information about the technology at this ITMA. The machine employs a new method of yarn separation from the upper and lower warp sheets. Two conical-shaped separators are used instead of the traditional method of yarn separation, which requires a range of needles depending on yarn type and size. The TIEPRO conical yarn separation mechanism is independent of yarn type and size. Additional features of the TIEPRO include: tying-in with or without lease; 3 to 100 Ne yarn count range; double end detection; short knot fringes; up to 600 knots per minute depending on yarn characteristics and size; and it’s suitable for staple yarns, 100-percent cotton yarns and cotton blends. TIEPRO is equipped with an Auto-Reverse function that is associated with detecting double ends. The machine repeats the yarn separating process on its own before tying and it does not cut the yarn. Operator intervention is required to separate the double end and then the tying-in resumes from where it was stopped.
Stäubli again exhibited its SAFIR 60 automatic drawing-in machines for striped warps. The company’s new version of Active Warp Control 0.2 (AWC 2.0) allows the SAFIR machines to detect double-end and manage color and S or Z twist sequence in instances of drawing-in warps without lease. If double-end is detected, the two yarns are returned to the warp sheet and the system tries again for picking one yarn. As for the color/twist sequence, the AWC 2.0 checks the yarn color against the color repeat sequence and if the yarn is out of sequence, it will be kept in a storage area. Yarn in storage will be picked up later and placed in the correct sequence. The color detection system is designed to detect small differences in color to meet the demand of using same color of different shade and depth. Weaving
Germany-based Lindauer Dornier GmbH exhibited the new air jet A2, as well as its rapier P2 weaving machines. The P2 rapier weaving machines were shown at ITMA 2015 before commercialization, and at ITMA 2019 post commercialization. At the Dornier booth, one P2 Type TGV 8/S G20/360 cm with 339 cm width in reed (WIR) machine was weaving plain weave sailcloth fabric at 320 picks per min (ppm) or 1,085 meters per min (m/min) rate of filling insertion (RFI); while an A2 Type AWS 4/E D 10/280 cm with 266 cm WIR was weaving plain woven awning fabric at 900 ppm or 2,394 m/min RFI. At the VANDEWIELE/Bonas booth, a second P2 Type TKN 8/J G/220 cm with 171 cm WIR machine was weaving intricate jacquard scarf fabric at 400 to 450 ppm or 684 to 770 m/min RFI; and on the Stäubli stand, another A2 Type AWS 6/J G/240 cm with 226.5 cm WIR machine was forming jacquard high stretch sportswear fabric from warp and weft yarns containing spandex at 1,000 ppm or 2,265 m/min RFI.
The A2 air jet machines, which is the successor of A1 series that was introduced in 1989, were shown for the first time at this ITMA. The A2 machines are highly digitized. The ErgoWeave® operating panel was redesigned with optimal continuous fabric production parameters overview. The more user-friendly high-resolution interface permits monitoring and shortens changeover of woven fabric parameters.
In the vein of digitization, weaving machines may be networked using Dornier DoXNet software, which provides a user-friendly production overview. Networking does not require internet; hence weavers have full control over their proprietary production, optimum machine settings and fabrics’ specifications data. With DoXNet, the optimum machine setting for a given type of fabric can be shared with other machines weaving the same fabric. If so desired, Dornier DoXWeave’s control desk, which centrally man-ages weaving machine data in a plant or plants, allows remote access to weaving machines’ production data. The Dornier myDoX is a portal that allows customers to shop 24/7 online and provides direct Industry 4.0 connection to experts and information from Dornier. Discussion with technical personnel at the show revealed that Dornier’s biggest contribution to sustainability is designing sturdy machines work for many years. Dornier still provides spare parts for machines produced in 1978. It is well known fact that weavers have to surplus their machines or seek machine shops for support at extremely high cost because of a lack of spare parts for early machines. The question that comes to mind is “Can such machines be digitized at reasonable cost to benefit from digitization and readiness for Industry 4.0?”
Itema S.p.A., Italy, unveiled the new EVO Series rapier machines, R9500EVO, and an air-jet machine A9500EVO. A total of 12 machines —11 EVO 1 R9500-2 and one Hercules— were in operation at ITMA; seven machines at its booth and five machines on partner’s stands. The machines covered the formation of diversified fabrics for apparel, home textiles and technical textiles using natural and high-performance fibers. At its stand, Itema exhibited R9500 EVO/220 cm weaving wool fabric at 600 ppm or 1,320 m/min RFI, R9500EVO/220 cm weaving denim fabric at 750 ppm or 1,650 RFI, R9500EVO/190 cm weaving jacquard tapestry fabric at 600 ppm or 1,140 RFI, R9500EVO/260 cm weaving jacquard terry fabric, R9500EVO/220 cm weaving reinforced sail fabric at 600 ppm or 1,320 RFI, A9500EVO/190 cm weaving bottomweight fabric, and Hercules/380 cm weaving heavy-weight filter fabric.
The five machines exhibited at other stands include R9500EVO at the Stäubli booth weaving Jacquard high fashion apparel, R9500EVO at the VANDEWIELE booth weaving Jacquard decoration fabric, R9500EVO at the MEI stand weaving label fabric, R9500EVO at the Julibao booth weaving label fabric and a R90002 weaving shoe fabric.
In terms of sustainability, Itema offers the mechatronic device iSAVER® for raw material waste reduction, which has been expanded to several other fabric types after its initial success in denim weaving. At the Itema booth, three machines were equipped with the iSAVER® device. The technology eliminates the need for auxiliary selvage yarns and cutters and minimizes the fringe on the left-hand side of the fabric. The iSAVER® is compatible with up to six different filling yarns.
In terms of digitization, Itema offers iKNOW™ and MyWeave™ systems. The iKNOW is an expert system loaded with information collected from the field over years. Itema reports the system enhances the user experience and optimizes production. Such systems are useful based on previous experience and therefore may be limited when it comes to developing new fabrics using new materials, especially fabric from recycled and bio-based fibers. The system needs continuous update that requires commitment from Itema and their customers. MyWeave is a new system that provides monitoring and management production data for a plant or plants. The EVO series is equipped with an EVOConsole of 15.6-inch-wide touch screen and can be connected to Wi-Fi and Bluetooth. It is also ready for data analysis and IoT. The EVOConsole allows access to the brand-new customer portal HelloItema, which allows customers to request service, access data and documents, and order spare parts.
Picanol NV, Belgium, unveiled new rapier Ultimax weaving machines that build on the predecessor Opti-Max machines. The Ultimax machines are designed with a high degree of digitization to facilitate operation and communication with each other, as well as PicConnect. Picanol also exhibited the OptiMax-i rapier and OmniPlus-i air jet machines that were shown previously. A total of 10 machines were shown at the Picanol stand, one machine was exhibited at the VANDEWIELE/Bonas stand and one at the Staubli booth. The list of machines along with fabric type, weaving speed and RFI are listed below:
The OmniPlus-i Connect-4-P-190 weaving machine was weaving bottom weight fabric from 100-percent recycled warp and weft yarns with fiber content 67-percent polyester/33 percent cotton at and impressive speed of 1,500 ppm (2,850 m/min RFI). The performance, and hence weavability, of yarns from recycled fibers is lower. Despite this, Picanol demonstrated the commitment to develop high-speed machines to handle such yarns containing short fibers and support sustainability initiatives. Picanol reports that the Ulti-max-4-R-220 is recycled yarn ready. Another notable achievement is weaving sheeting from fine cotton yarns Nm 102/1 warp and Nm 68/1 weft with fabric count (72x41x2) at 1,000 ppm weaving speed or 2×3,400 m/min RFI — the 2 denotes double-pick insertion. As a result of the higher levels of short fiber content in recycled yarns, higher fly is generated that settled on the machine, warp sheet and fabric during demonstration. This fly will require a blowing system to remove the lint. Blowers and suction systems are not unusual in weaving operations.
The Ultimax-8-R-360 and Omni-Plus-i Connect-4-P-190 machines were equipped with newly developed leno motion O-Leno. The O-Leno yarns are driven by a timing belt and two time gears that can be programmed to form half-turn or full-turn leno weaves to secure the fabric selvages. It may be programmed to vary form half- or full-turn leno for individual weft yarns depending on their surface characteristics.
Picanol’s highly digitized machines are Industry 4.0 ready. The company developed PicConnect to access data stored in the cloud. It is the gateway to all Picanol digital information access such as Picanol applications, IoT, AI, and customer service.
Smit S.r.l. Italy, exhibited three rapier machines — the new 2FAST 220 C8 D; the GS980 260 F8 J, previously shown at ITMA; and a new conceptual machine under development, the CONCEPT 190 C8 D. The 2FAST machine was weaving denim fabric at 700 ppm with WIR 222 or 1,554 m/min RFI, the GS980 machine was weaving jacquard terry towel at 500 ppm with WIR 244.4 cm or 1,222 RFI, and CONCEPT machine was weaving shirting fabric at 800 ppm with WIR 172 cm or 1376 m/min RFI. The 2FAST and the CONCEPT machines are designed for quick style Changes. The warp stop motion of the CONCEPT machine uses a laser device, which eliminates the drop wires. Monitoring warp breaks using lasers may be challenging in situations where a high warp density causes the broken yarn to be supported by neighboring yarns instead of falling where it is detected by the laser. The 2FAST machine is equipped with 2SAVE that was shown for the first time at ITMA 2019. 2SAVE eliminates auxiliary selvages from both sides and cut weft fringes collected for recycling. While the machine at the show was weaving denim fabric, it is designed for versatility to weave fabrics for fashion, home textiles, and technical fabrics using range of yarns from different fibers and counts. The rapier uses a previously introduced free flight system — no guide is required to support the rapier during weft insertion.
Japan-based Toyota Industries Corp. showed three of its new JAT 910 air jet series machines at ITMA. A JAT910 4F-230ES-EF was weaving high fabric count (274×526) double-faced fabric at 1,000 ppm with WIR 210 cm (2,100 RFI), a JAT910 2S-340LM-ET was demonstrated weaving side-by-side 261 cm wide sheeting and 20 cm wide pillow fabrics at 900 ppm (3,060 m/min RFI), and JAT910 8T-280JE-EH was weaving four panels of different jacquard terry towel patterns at 950 ppm with 269 WIR (2555.5 m/min RFI). Toyota’s approach to sustainability is in reducing air and energy consumption. Its i-SENSOR technology monitors the leading weft yarn during insertion inside the shed prior to arrival at the right-side selvage. Early arrival — which occurs as the weft package diameter is reduced due to the fact that the weft yarn gets more air friendly with higher traction —will be detected and insertion timing is adjusted accordingly. Toyota reported a 20-percent reduction in air consumption compared to the conventional models. There are no studies in public domain that com-pares air consumption using adaptive control systems by different machine manufacturers.
Toyota’s factory management support system FACT has been evolved to FACT-plus. The system collects data in real time from weaving preparation, weaving machines and the inspection room, and pro-poses actions to machines and operators. It monitors different sensors — such as speed, pressure, temperature, and compressor pressure data, for example — and provides instructions for machine maintenance and the next assignments for operators.
Japan-based Tsudakoma Corp. exhibited a new air jet weaving machine series, the ZAX001neo, that was successfully commercialized and sold in 2021. At its stand the company demonstrated a ZAX001neo-190-2C-Cam weaving lining fabric at 1,200 ppm (2,280 m/min RFI), and a ZAX001neo-390-4C-Cam weaving awning fabric at 820 ppm (3,198 m/min). A new weft insertion system, designed as a standard for the ZAX001neo machines with optimized auxiliary nozzles positions, led to a reduction of 35 percent in air consumption corresponding to 20-per-cent reduction in air pressure compared to the previous generation model. Additionally, a direct drive high-efficiency IPM motor, developed for this series, reduces stop marks. The company upgraded its weaving support system to Weave Navigation® System II. The system has different functions: Weave Vavi® provides user support to best weaving conditions for a given situation; Tune Navigation delivers the best machine setting — including loom timing, tension, easing amount and air pressure — for a given fabric type; and i-start, which eliminates stop marks via controlling the let-off and take-up to adjust cloth fell position and the warp tension back to its pre-set levels.
3D weaving for fiber-reinforced composites and other innovative applications was a highlight in the weaving area again at this ITMA. At previous shows, companies displayed 3D woven products with variable thickness, distances (spacer), stitched multilayer, and unstitched/stitched double cloth for insertion of electronics and ceramic for ballistic protection.
At ITMA 2023, VANDEWIELE showcased samples and displayed on a large screen several distance/spacer fabrics for automotive and boat applications to demonstrate the capabilities of its weaving technologies.
England-based Optima 3D was a return exhibitor at ITMA. The company exhibited one Series SJ-600-4 3D weaving machine equipped with four shuttles for weft insertion and the SX Staubli Jacquard shedding system. The machine forms one shed at a time and the shuttle is transferred by a magnetized rapier arm for weft insertion. The arm is designed with a magnetized conical space to hold the metal nose of shuttle. The machine is equipped with a linear fabric take-up motion — thick 3D preforms cannot be taken-up on rollers — and touch-screen controls for user interface. Warp yarns are supplied from a com-pact creel with rotating flanged spools that allow parallel winding for longer yarn packages and hence longer runs to reduce creel changes. The creel capacity is 576 spools, and two or more creels can be set behind the machine if needed. The company product line also includes spool winding machines. Shuttle weaving combined with a jacquard shedding system allows the formation of 3D orthogonal and angle interlocking, stitched/unstitched multi-layer along with a variety of shaped 3D preforms including I, T, Truss, cellular, among other shapes, for fiber-reinforced composites and other applications.
VÚTS A.S., Czech Republic, exhibited the DIFA air-jet weaving machine weaving 3D distance fabric. The machine can be programmed to form fabrics with variable distances between the top and bottom base, or ground, fabrics to obtain the target shape of the inflatable structure after coating. This type of distance fabric requires a mini-mum of two warp beams — one dedicated for the warp sheet for the top and bottom ground fabrics and the other is assigned for the pile warp sheet. Applications for the distance fabrics include inflatable structures such as boats of different types, dock, mats, flood protection and lifting bags.The company also showed its CAMEL ADAPTIVE air-jet machine for leno fabrics. VUTS promotes its machine as Industry 4.0 ready.
Switzerland-based Jakob Müller Group has been developing narrow weaving machines for smart textiles applications since ITMA 2011. Back then, the company showed a wireless smart label that consisted of a woven antenna from electrically conductive yarn and a chip with integrated circuit for antifraud identification using radio frequency (RF) technology. At ITMA 2019, the company showed its NFM®MDW® — Multi Directional Weaving — machine weaving narrow fabric containing electrically conductive e-yarns from polyester/copper/silver with the aid of e-yarn guides that move the yarns out of the open reed and place them as desired to form fabric-based electronic circuits.
At ITMA 2023, Jakob Müller showed the NFM 53 2/84 MDW. Unlike the previous generation shown in 2019, the updated model uses a different methodology of laying in effect or functional yarns in strategic places to form a desired pattern. The MDW is equipped with effect or functional yarn guides with up to four guide bars available. The effect/functional yarns are moved downward aided by the guide bars. The weft yarn is then inserted to hold the effect/functional yarn in place, then the effect/functional yarn is incorporated to the fabric following the beat-up. A strategic motion can be electronically preprogrammed to move the effect/functional yarn to either side by a specified distance and lower the yarn to interlace with the weft yarn. The steps are repeated to complete the targeted design. The calculated movement of the effect/functional yarn guides results in the formation of area covered with the yarn distributed with the desired pattern. The NFM 53 2/84 MDW machine was demonstrated forming an e-textile from polyester filament base fabric yarns and two conductive yarns containing copper and nickel controlled independently by two guide bars. Potential applications for this technology include e-textiles, fashionable textiles using colored and fancy yarns, and multidirectional yarns for enhanced performance in different directions other than the main directions of warp and weft. Currently, formation of 3D multidirectional preforms for fiber-reinforced composites is achieved by manually stacking of 2D woven fabrics at different angles to form semi-isotropic and other structures with enhanced properties at different directions, which is time consuming, subjected to labor errors, and costly. The MDW technology can be expanded for broad weaving to benefit the fiber-reinforced composite industry for forming wide preforms with laid-in multidirectional high-performance yarns.
On-loom fabric inspection systems have been developed to detect defects at the loom stage and trouble shoot the root cause of defects and thus avoiding the production of off quality fabrics that leads to reduction in fabric waste and increase in profit. One of the early systems was Batch Motion consisting of an off-loom fabric take-up, platform/stage for operator/inspector and inspection station. The inspection station is similar to post-weaving manual inspection and relay on the weaver/ inspector’s eye to detect defects. There are several drawbacks associated with the batch motion and to eliminate manual or Batch Motion inspection, several automated on-loom fabric inspection systems with high-speed image capture using cameras and scanners were developed. Examples of these technologies include LOOM-TEX by Elbit Vision Systems, Israel, Cyclops by Duluth, Ga.-based Barco, and Fabricscan by Uster Technologies Ltd., Switzerland. These systems can capture and store fabric defect images, identify and classify defects, report defects maps, and stop the weaving process based on the severity of the defect. The systems are installed between the front fabric rest and take-up rolls, which was an improvement over the manual post-weaving and Batch Motion inspection. However, more than one meter of fabric passes the system before detection, which results in late discovery of fabric defects and leads to second quality product and waste. To avoid this serious disadvantage, Uster offers the Q-BAR 2 on-loom automatic fabric inspection system that was exhibited again at this ITMA. The scanner is installed right above the fabric formation area and covers the entire width, including the cloth fell, as well as the fabric length as the fabric is taken up for 100-per-cent quality fabric quality monitoring. The fabric is scanned right after each weft insertion so fabric inspection is not delayed. The Q-BAR 2 is equipped with a touchscreen visualization system. The system offers options for grading fabric rolls based of defect type, size, and location that can be defined based on the quality required in the end-use product.
While there are high volume instrument systems to measure fiber quality data that spinners use to optimize bale layout for production of high-quality and consistent yarn batches and monitoring quality of yarn of individual positions on winding machines, these data are not utilized by the weavers due to lack of available systems. Warp yarns are numerous and it is extremely difficult to make use of their quality data captured during the winding process during the weaving process. It is envisioned that the Uster Q-BAR 2 system may be used to monitor the warp yarns. Two monitoring locations may be feasible: to monitor the warp sheet between the warp take off point from the warp beam and web roll using additional unit; or, to monitor the warp and fabric quality using one unit. The latter approach is less expensive but more challenging as the reed moves — from the beat-up position to the most back position —and comes between the scanner and the warp sheet up to 1,500 times —equal to loom speed in ppm. However, this may be accounted for since the system uses high-speed cameras.
The ultimate goal of Industry 4.0 is to maximize productivity, efficiency and product quality through automation and digitization of technologies that allow communication between machines, software systems, and people via the Internet of Things throughout different stages of the pipeline required to manufacture a product. This can be achieved by cyber-physical systems and big data/cloud storage to collect data from sensors and integrate them for analytics and artificial intelligence (AI). In terms of automation, weaving machine manufactures have developed numerous automated systems including warp stop motions, weft stop motions and automatic repair, monitoring stops and efficiency, adaptive weft control systems for air-jet weaving for saving energy, automatic weave/pattern change, pre-programmed weft selection for intricacy and hybridization, preprogrammed variable machine speed, preprogrammed weft density, automatic on-loom fabric inspection, automatic smart drawing-in and tying-in machines, individual warp yarn control in jacquard, and individual harness control in dobby, among other automation technologies. More affordable automations are still required to achieve the goal of Industry 4.0, including automatic repair of broken warp yarns, multi-phase weaving that triples or quadruples productivity with dobby/jacquard shedding systems, and automated style change system. There is a need for integration of the entire technologies required to manufacture woven-based products from fibers since the productivity and quality are influenced by all the steps required to form them.
At this ITMA, weaving machine manufacturers continued to advance their technologies with high degree of digitization that allows machines to communicate and store big data relevant to the production and fabric quality that are accessible to users via intuitive use-friendly interface. Manufacturers’ software products are broad and varied, which poses challenges to companies housing machines from different manufacturers. Machines are driven digitally by proprietary and elaborate low-level computer code. A company with machines from different manufactures cannot integrate its production and quality data without adding significant cost. The integration must be done by collaboration between machine manufacturers to standardize data access and user interface or by a third party. The demand from customers may lead government agencies to regulation of standardization. Collaboration between companies that are not fully vertically integrated, such as greige fabric producers, are in need to collaborate with their suppliers and customers to take full advantage of digitization and Industry 4.0.
The complexity of the textile industry creates a need for a technical team with collective skills in textile technology and engineering, machine learning, AI models, computer programming language, mathematics, and statistics to achieve the goals of Industry 4.0. Vertically integrated companies may afford to build such a team. Those who cannot afford such a team may collaborate with their business partners or retain consultant firms in the field. How fast the textile industry completes the road to Industry 4.0 depends on the factors discussed above and perhaps more importantly on the economy.
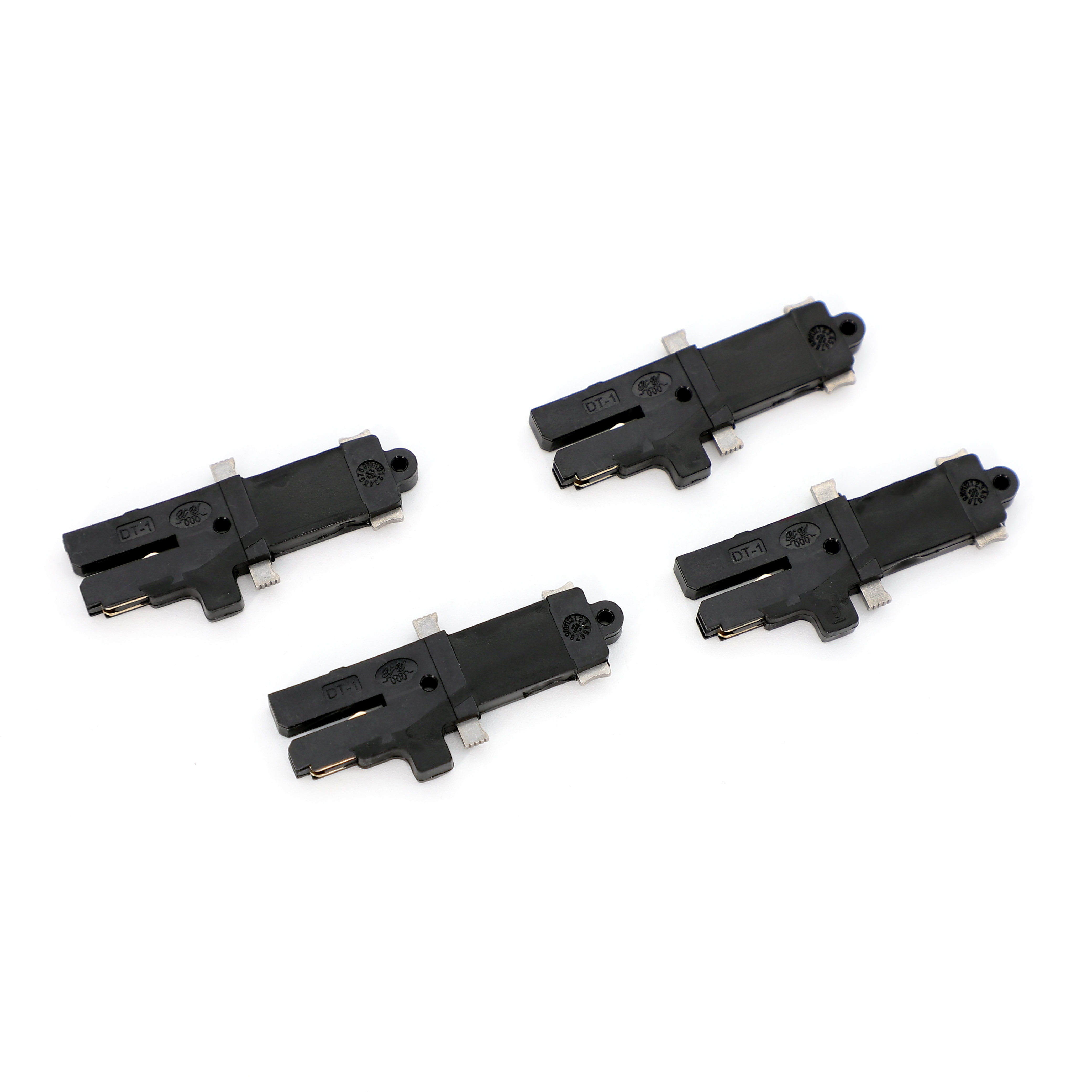
Edgar Watches View Latest Digital Issue »