For one-off projects or prototyping, it’s not too hard to find a wall wart or power supply to send a few joules of energy from the wall outlet to your circuit. Most of these power supplies use a transformer to step down the voltage to a more usable level and also to provide some galvanic isolation to the low voltage circuit. But for circuits where weight, volume, or cost are a major concern, a transformer may be omitted in the circuit design in favor of some sort of transformerless power supply.
While power supplies with this design do have many advantages, some care needs to be taken with regard to safety. The guide outlines four designs of increasing complexity which first puts out a basic transformerless power supply, using a series capacitor to limit current. To bring the voltage to an acceptable level, a recognizable bridge rectifier is paired with a capacitor as well as a zener diode. The second circuit presented adds voltage stabilization using a transistor and 78XX regulator. From there, zero-crossing detection is added to limit inrush surge currents, and the final design uses the venerable 555 timer to build a switching power supply. Transformer

Although it is noted several times throughout the guide, we’ll still point out here that transformerless designs like these introduce several safety issues since a mistake or fault can lead to the circuit being exposed to the mains voltage. However, with proper care and design it’s possible to make use of these designs to build more effective power supplies that can be safe to use for powering whatever circuit might energy but might not require the cost or weight of a transformer. For more on the theory of these interesting circuits and a few examples of where they are often found, check out the shocking truth about transformerless power supplies.
Thanks to [Stephen] for the tip!
** Your circuit ground is directly connected to the AC line **
Depending on the use, this can be fine, but remember, if you have a 2 pin reversible plug, that means that your circuit ground can be at 120VAC
Alternately, if you live in a place with a 240 volt system that uses a split supply, your circuit ground ** always ** has 120VAC relative to earth ground
With that warning out of the way, enjoy.
LOL. 120Vac. Go play with your toy voltage in another room.
We have both 120V and 240V in the US. My washing machine, dryer, and stove all run on 240V. The reason we have 120V is because A) it’s safer than having 240V in all sockets given our plug design and B) we’re working with backward compatibility from when mains power was first invented in the United States.
Same story with NTSC vs PAL; when you make something first and then others make their own, improved versions of it, they get to benefit from hindsight you did not.
The “we have both” comment is very misleading, because in pretty much all of europe we have single phase 230V, and two/three phase 400V. Homes often have all three phases, but split into different parts of the home to split load on 230V circuits. Most houses in villages, or industrial buildings have three phase 400V sockets for powering heavy equipment, like circular saws, welders and others.
So any way you cut it, the EU power system can still deliver more power.
People have died from contact with 120VAC . Not sure why to talk about toy voltage. Seems like lack of experience.
Yeah, this is ideally NOT safe. But you can get away with it – if you are lucky.
220 -240v in many countries.
Correct me if I’m wrong, but I was under the impression that most of the 240v countries (which is to say, most countries) us a split system with two ‘hot” legs, each of which is at 120v, with 180 degrees between them, so that the absolute voltage relative to earth ground is never more than, say, 170v peak.
This is also mostly the North American system, but we only use only one leg at time on the smaller 120v outlets, so we also have a ‘neutral’ conductor, basically the center tap, which is tied to earth ground at the service entrance. In this system we also see a 170v peak.
I also seem to remember that UK pattern systems have a true 240vac relative to ground, with one hot leg and one neutral leg near earth for a 340v peak on the live side. This seems like a lot to me for domestic service, but people there don’t seem to die at an elevated rate, so I’ll shut up now.
All these systems function just fine, but it does raise interesting questions when you start talking about supplies that are not isolated from line potential.
No, this is not true. All 240 volt Mains countries use 240 volts phase to ground. Typically homes will either be supllied with one leg from a 240/416 volt three phase transformer, or have all three phases brought into individual homes to supply both 416 vac three phase equipment and 240 vac single phase equipment. Split phase systems only exist in 120 vac mains countries, and possibly Japan with their 100 vac mains, though I am less sure about them.
It also we doesn’t matter whether it’s 240V to neutral or 120V to opposite-phase 120V. The circuit operates on the difference between the line inputs. By
Think you have dropped conclusions a little here. To summarise, in domestic applications you’ll 240vac rms , the live being 240 and neutral 0. However saying that in industrial applications to reduce cost or going over some limitations where you don’t have a neutral going in to you panel you can opt to phase to phase step down transformers that will then give you the 120vac per phase (dual phase). Yet again you must not confuse dual phase to single phase. Hope this helps.
No, most 230VAC single phase systems have one phase clamped to ground therefore a phase, neutral and ground.
Let’s see, what happens if two of these are in use and plugged into the wall opposite of each other. And then the minus poles touch? Let’s just watch the excitement.
Nothing will happen, these are not wall warts. Since these circuits are only used as internal power supplies in Class I and Class II appliances, no way to directly connect two of them exists.
They may be INTENDED for internal PSUs, but that doesn’t ensure that is how they will be used. It isn’t as if things seen on HaD aren’t applied to a wide variety of things they were not originally intended for.
Many readers may see this as an inexpensive way to power some µC controlled project – automatic blinds or whatever – and those may be connected, if only occasionally for firmware updating via a cable, to a device with an actual ground (or subordinate to a controller with a similar supply, but wired opposite, or even from another split-phase circuit powered from the other half of the split phase, etc). For some double-insulated project with no connection whatsoever to anything else, these are IMO, no more dangerous than anything else plugged into a wall outlet. So long as it remains closed and has nothing that you plug into it.
I use non-isolated mains for some projects (usually involving switching mains, so it’s not as if there isn’t line voltage in the box), and near the programming header on the PCB, I have silk-screened text warning to disconnect power before programming due to the lack of isolation. If I were more clever, I could have oriented things such that the terminal block for connecting the supply had the wires coming in over the top of the pogo landing for programming such that you would HAVE to remove the power in order to reach the programming header. However, those projects are for my use, not for sale.
TI’s UCC28881 is an off-line switcher capable of switching from up to 700V. No isolation (though there are application examples with flyback transformer, the basic circuit has no transformer). These are excellent for projects which are not particularly current hungry, and also, since they’re switching post rectification, they can run from DC sources such as a PV module.
There’s a reason no certification agency would ever approve a design like this.
Of course, if you put a line isolation transformer in front of it, no problem at all! But that sort of defeats the purpose, doesn’t it.
No such thing as a free lunch, unless you don’t mind the corpses littering the dining table.
A circuit very much like that is inside every 120V LED light bulb being sold today. Now, it might have been prudent for the author to mention that this circuit cannot be used in any context that connects other devices to devices being powered by this, nor should any circuit powered by this have less than two independent layers of insulation between itself and any human, but the circuit itself is safe enough when used within these constraints.
I just checked, and I see the UL label on one right in front of me.
My dishwasher (at least, and probably other appliances) runs its internal electronics from such a ‘hot’ power supply. If the entire circuitry is physically isolated from the ‘outside world’, I see no problem. Or dead people.
No S. Katz, it’s a very normal mode of operation …but only for products which will not have any metal parts accessible to the user. There does need to be a fuse..often the series resistance is rated as a fuse. As others have said, LED lamps, night lights . Remember back in the day of Valve Tube radios And TVs, a potentially live chassis was rather common.the difference was that any switches and potentiometers were thick Bakelite knobs and the shafts were also plastic and they had no auxiliary outputs.
These supplies are really dangerous, particularly to line transients… and jeez, the schematic doesn’t even show a line fuse! So if any capacitor or the bipolar transistor blows, this thing goes up in a flash, on top of shock hazard.
Making a switching power supply is no skill, but making a *good* one is.
The amount of work needed to make a clean, powerful switching-PSU could also be saved by just using a humble transformer PSU.
That’s why high-quality lab PSUs on transformer basis still exist, after all. They’re a lasting piece of equipment you can depend on. An investment for the future.
efficiency, eg. for running on battery, transformers are less desirable.
Transformers are *not* inefficient. They’re actually pretty much the single most efficient way to convert one AC voltage to another. The inefficiency can come from impedance mismatches and switching loss in the semiconductors. Capacitive switching regulators (called charge pumps) do exist, but they tend to have poor regulation in comparison, and real capacitors are not as close to the ideal circuit model as inductors/transformers.
That being said, for a battery a buck-boost architecture would generally be used since the voltage is already low.
Short version: transformers can multiply or divide their input voltage by a constant ratio “for free” (with some very minimal resistive loss). While high voltage switching components (transistors and diodes) do exist, switching loss increases dramatically due to parasitic effects and heat. It is often much more efficient to use a few of the larger components to “chop up” an incoming waveform (AC or DC) and pass it through a transformer, followed by a much lower voltage switching or linear regulator stage. The other major benefit is that transformers can have multiple taps, allowing multiple outputs at different voltages.
As a German, I would agree that efficiency is important. But quality even more so. That’s why my vote goes for the transformer in this case.
Battery operation is an exception, maybe. But even here, I’d opt for technologies proven by time. Say, a lead battery over LiFePO4. Because, the additional electronics of the latter is an uncertain factor that’s not been thoroughly tested yet.
Bit of a weird comparison. Lead batteries have real and very much understood disadvantages in their chemistry that make it pretty much unsuitable for most use cases of where you would want a battery.
And they still need electronics, especially if they aren’t tied to a constant power source and you want it to last awhile.
Another thing you must consider is true galvanic insulation, my friend. A transformer can met this criteria.
This includes the small transformer in traditional switching PSUs, too.
Those newish designs with DC-DC converter ICs are to be taken with care.
A common ground connection between input (AC main) and output (DC) is dangerous and a bad design.
The ground of the AC mains should never be connected to the chassis! That breaks the whole concept of galvanic insulation.
Protective earth is a special case, of course.
In the old days the ground of AC mains _was_ connected to the chassis. My old B&W valve TV’s did this.
It is inefficient when the load is low, for example in standby.
I always use a transformer lump for psu projects simply because if I give it to a friend or relative to use…I still want them to be my friend or relative when the day is over😯
The “humble” PSU will be much more expensive, heavy, bulky.
And they’re fixed-voltage, you have to have one for every voltage. Switching PSUs are much more flexible.
Is it just me or is this design horrendously inefficient? It’s essentially a rectifier followed by a linear regulator dropping HUNDREDS of volts. I guess it’s fine if you just a couple mA. for sensor or something.
when loaded much of the voltage drop is over the input cap, that’s what it is there for
It is. It’s why they aren’t used in commercial designs. I learned this design long ago as a quick way to reduce voltage with output limited to only a couple hundred mA
You’ll find the combination of a capacitive dropper and a (sometimes amplified) zener diode in many household appliances, e.g. the temperature display/thermostat for a fridge or the power control for a vacuum cleaner. If designed correctly, efficiency is at least as good as a small mains transformer or SMPS.
I was about to add the same comment. I took my coffee kettle apart the other day, all the digital electronics is powered this way. There is a three pronged plug, the digital ground is AC neutral, and the base is entirely plastic. It’s safe as long as the AC socket is not wired incorrectly.
The only concern I had was the rotary encoder, which has a plastic knob, also has a metal shaft and the metal shaft of the encoder was left floating and I would have liked it to be grounded, just in case it ever comes in contact with a loose, hot wire, or mineralized water overflows and got into the guts of it all.
This is extremely dangerous. Do not build this circuit. Shame on hackaday for placing this on their pages. Anyone with enough experience to build and operate this supply safely while know better then to do it anyway.
If you’re working with mains you should know you might (will?) get zapped. It comes with the territory. I’ve built similar circuits before (and gotten bit by them) and I’m still alive. Stop crying.
https://en.m.wikipedia.org/wiki/Survivorship_bias
I agree. There can be a lot of unknown unknowns when implementing circuits you see in internet and each of them might end up being fatal. Usually in the literature I’ve seen long list of rules about doing stuff with mains first and example circuit after that. And also mentions that only qualified professionals should do it in the first place.
If you know enough about mains, designing that kind of circuit is something you can easily do yourself and plan sufficient safeguards at the same time.
Power supplies like this come in single chips like MP150 on LNK302. They are used all over in IOT products.
The circuit in the image above: What is the point of first doubling the input voltage (using a Greinacher voltage doubler) (up to 340VDC) only to have it regulated down to 80VDC?
Because the design is ment as a LED power supply, for a long string of LEDs. So 80v is the low end of what the supply can provide. For a higher voltage, you can just change the zener to the voltage that you desire. Also the voltage wouldn’t go all the way up to 340v if you have 120v mains, right? So this makes the design both 240v & 120v mains compatible.
I believe the function is not to double the voltage, but to unload the capacitor. It’s not possible to pump voltage just one way in a cap, you need to also include it in the circuit in the other half wave. If the second diode was not there, you’d see negative 680 v across the series diode in the negative half cycle. Or -340 on you side of the pond. It would double the voltage, but with the zener and a load it will not.
Many (probably most) transformerless wallwart power supplies put out their rated voltage only under the load they were intended for. The no or light load voltage can be considerably higher (peak versus RMS) and zap unsuspecting gear. I never throw away a wallwart and have a large box of them. I recently went through all of my 12 VDC wallwarts (about 15 of them) and only found two that were close to 12 volts with no load. I was surprised to find even two, and they turned out to be originally intended for name brand gear.
That used to be different in the 80s/90s here in Germany. We had stabilized/egulated power bricks with a transformer. They had an power LED and a switch for selecting multiple voltages (3v, 4.5v, 7v, 9v, 12v AFAIK). Output was DC, of course, using a more efficient bridge rectifier design. Some had internal fuses, too.
Then, after 2000, the CE sign came and with it lots of poor switching PSUs from China. They flooded the market, caused trouble due to lower quality power (ripple!) and RF noise (RFI/TVI/EMI).
They also were deadly, because ground was on both AC/DC. Lots of teenagers wouldn’t have died in the bathtub while charging their phone, if transformer PSUs were still in wide use these days. Everyone, please think about it.
These transformer power supplies were usually not stabilized (although stabilized ones also existed), and the voltage was selected by switching the pins of the transformer’s secondary winding. The current rarely exceeded 300-500mA.
Transformerless supplies are okay for low power solutions where cost is the most important thing. Also these supplies require to be completely sealed in the project, so there is no risk for the user to be exposed to their output. That’s why even the cheapest chargers use a transformer, to provide at least some tiny bit of safety during normal operation.
The only time I used a transformerless supply was to light a single LED in a device, that showed it was switched on. Alternative was using a quite beefy resistor or simple current limiter to drop ~68V at 10-25mA. That’s 680mW at least to make a light.
If you need more than 50mA of current, then get a transformer. There are plenty of somewhat cheap ones, and you can get one from an old wall wart, too. I saved two or three antenna power supplies with damaged cables because each of them has a nice 12V 1,5VA transformer. Good enough for some analog fun.
Better select a safety capacitor for the 3uF 400V that’s in series with the mains. Otherwise, the circuit becomes unsafe if/when that capacitor leaks or shorts.
As other readers have pointed out, this circuit is just not safe. A non-polarized plug or an outlet installed backwards and boom, the ground is hot with absolutely nothing but the breaker in the mains panel to limit current. You could literally kill yourself.
Back in the day, circuits like the “All American 5” tube radio pulled a similar dangerous trick. “Death caps” in guitar amplifiers that could short or leak making the floating ground hot also come to mind. I recall a Silvertone guitar amp that earned the name “widow maker” because of its lack of transformer isolation plus a “death cap” for EMI suppression as a bonus means of zapping yourself into the next world.
Transformerless supplies have been used by the millions in consumer products where the design makes *sure* that no one can touch any part of the circuit. You find them in radios, TVs, clocks, LED lights, and all sorts of appliances. The supply, and whatever it is powering are in the same box, and that box is designed to have no exposed metal. There is also a substantial insulation gap between any internal metal parts and any external parts the operator can touch.
Transformerless supplies can also be very efficient. One example has a capacitor in series with the AC input to drop the voltage between line voltage and the desired output voltage. This feeds a thyristor regulator (i.e. a TRIAC with a zener between its gate and anode). The waveform across this combination pulsates between +Vzener+1v and -1v. This is halfwave rectified and fed to a filter capacitor. The resulting filtered DC voltage is produced with essentially no losses. In effect, it’s a 60 Hz switching regulator.
As in many things, safety is a consequence of paying attention to all the details.
Hello Lee Good to see you or hear you. I thought you were as old as I am. Didn’t see anybody mention the Manzanita micro electric car charger here. My first thought while reading all the safety concerns is why not put a capacitor on both sides of the AC line. What name would we give this a bad boy charger with manners and a capacitance to do some mischief?
The article says people unused to working with AC should be careful because you don’t have the transformer for galvanic isolation. But if someone doesn’t know which wires not to touch, they’re not safe with a transformer, either – especially if advice like this makes them think it’s intrinsically safe.
Mr. Cockfield, I’m sure you were just trying to be clever, but just so people don’t get the wrong idea, power supplies do not supply Joules. They supply Watts. Energy is power integrated over time, so it depends as much on how long you leave it on as on how much power it can deliver. Which is kind of useless unless you’re designing a battery charger and don’t care how slow it is.
I’ve done some work on certifying High Voltage power supplies. When there is not a separation from the mains, then the safety requirements get a lot more complex and detailed. Double insulation is required all around, other expensive safety required components. What would be real cool is a transformerless isolated power supply.
I can see various comments about polarized vs non-polarized plugs. But i’ve noticed that quite often some multi-plugs or even simple extension cords can inverse polarity between input and output! Even ones from reputable brands (like Legrand in France). So you can simply never expect polarity to be respected/trusted.
Dangerous voltages can show up in weird places… I’m currently working on an LT3752/LT8311-based flyback isolated DC:DC that’s being fed 28V DC in to 12V DC out. It is essentially the same as the 1994A eval card. In the course of debugging, I discovered I hosed the transformer polarity in the symbol and had to rework the pins to reverse the error, which fixed the “nothing coming out” problem I was having. So, having fixed that (holy crap what an ugly fix), I did some spot checks with a FLIR camera to look for hot spots. I found one in an unexpected place. Take a look at the 1994A reference design if you’re interested. It turns out, R48, the 20K resistor on the inductor snubber circuit, was the hottest component. In sim, the node only swings to 28V when the inductor switches off, as seen at the capacitor C30. 28V there would be dropping 16V over the 20K into the 12V output. That would be only 12.8mW, no problem for a big brawny 1206 resistor, right? Well… the FLIR was saying otherwise. So I measure the voltage across C30 to find 110V DC !! WTF?
Well, Linear Tech/Analog Devices did spec a 250V capacitor there for some reason :) The demo circuit is specified to accept up to 48V input and we were only feeding it 28V. It could be even worse…
110V at C30 draining through 20K into the 12V output (incidentally, the 12V under 1.2A load looked very clean). Well, V^2/R = (110-12)^2/20000 = 480mW. It’s a 250mW resistor. I think/hope this must be something related to the kludge fix on the transformer causing excessive inductive kick. So now I know why the 20K resistor was hot while every other component wasn’t even breaking a sweat. 4.9mA is draining across the resistor, a net 98V being dropped. Would you expect to see 110V in a 28V to 12V converter circuit? A quick search says 20mA across the heart is considered capable of causing fibrillation. Cranking the input voltage up to 48V might just get it to that level.
As an aside, I did find there are much higher power resistors available in 1206, up to 2W. Those get pricey, so I opted for the 750mW just in case, as it was a negligible premium over the typical 250mW. It should not need that according to sim, but just in case…
Not to downplay anything you’ve said. However, my background is medical. I know that during heart surgery they defibrillate at between 10-30 joules with direct placement on the heart itself. Otherwise defibrillation starts at 100 and maxes out at 360 joules.
While the body can certainly be a half ass insulator for the heart I’m not volunteering for that demonstration.
“… some care needs to be taken with regard to safety.” That may be the understatement if the year. This circuit is dangerous and can kill you if you are not very careful. This circuit is dangerous and can kill you if you are not very careful. (Repetition intended.)
“This circuit is dangerous and can kill you. Period” “This circuit is dangerous and can kill you. Period” “Repetition intended.”
zappy got me a few times I am definitly a saftey third kind of guy in general and find “saftey culture” abhorant,and when it comes to dumb asses dying while charging a phone thats fully approved as “safe”,I know that there is no argument to be made about this or that ,the other thing,bieng in any way better or worse or safe. How on earth is the thing not fused? design a wall wort that is truely fail safe and save your ire for the cleptocrats that will not then regulate it is mandatory for ALL domestic uses. We can call it rubber duckie approved and safe. After that is all taken care of,I need help rewinding the transformer in a Klempt guitar amp.
This design is transformerless, but that merely means that it doesn’t *depend* on a transformer. It works perfectly fine with a 1:1 isolation transformer in the input, and will function the same (but with more safety).
Using an isolation transformer in the input is a pretty common solution even in switching designs, as it ensures isolation and significantly reduces the hazards (downstream power is limited to whatever the isolation transformer can supply)
Series resistor required on the supply side to stop the series capacitor taking too much of a hit in the event of noise, spikes or harmonics on the line. Also, a bleeder resistor accross the high voltage cap. This stops that unexpected, post plug out zap. The bleeder resistor needs to not only have appropriate power raring, but also a high enough voltage rating. 1/4 w won’t do.
I’m starting to think these are the problem I’ve been having in my home. I have my Laptop at my desk, my old PC under my desk and my Microsoft Surface Pro 4. The Surface and Laptop are connected to the same power strip on my desk and the PC is connected to the same double outlet that the power strip is plugged into. That PC sometimes doubles as a leg rest. If I have my feet on the PC case and touch the chassis of the Surface, I’ll get, not just a buzzing feeling, but a bit of pain from it. Measuring the chassis to me, it’s around 80-100v. Not fun. Taking my feet off the PC and I’ll get a light buzzing feeling from the back of the Surface. It happens with the genuine and aftermarket USB-C GaN chargers too. I had some other dock that needed external power. Attempting to plug the dock into the USB port on my laptop resulted in sparks between the plug and laptop USB socket. Yup, same power strip. And finally about a month ago I had a micro USB cable plugged into a USB PSU that I charge some headphones with. By simply touching the end of the USB cable gave me a nice boot and killed the USB PSU. These things are getting stupid. And yes I have changed the power strip and the issues remain.
This is a completely different problem. All SMPS have an EMI/RFI filter at the input with the center point connected to the chassis. With Class I appliances (your PC), the chassis is connected to protective earth at the mains input. USB chargers are usually built as Class II (double insulated, no PE) and have the center point connected to output ground, so the filter also acts as a capacitive voltage divider that lifts the output ground to half of the mains voltage. The supplied current is very low and not harmful to humans, but it can kill electronic stuff and is a nuisance. You can fix this by using USB chargers with a PE connection (they do exist, mostly industrial stuff) or by using your PC as the only charger.
I know a guy who built a transformerless audio power amplifier. He used 6080 regulator tubes on the output (cathode follower as I recall) and a polarized AC plug so the ground was neutral. This was back in the 70’s.
Power supply regulators like this are fairly common in cordless power tool battery chargers, even from major manufacturers. If your charger doesn’t weigh 10 pounds and hum when operating, it’s probably got a circuit similar to this to drop the voltage.
Please be kind and respectful to help make the comments section excellent. (Comment Policy)
This site uses Akismet to reduce spam. Learn how your comment data is processed.
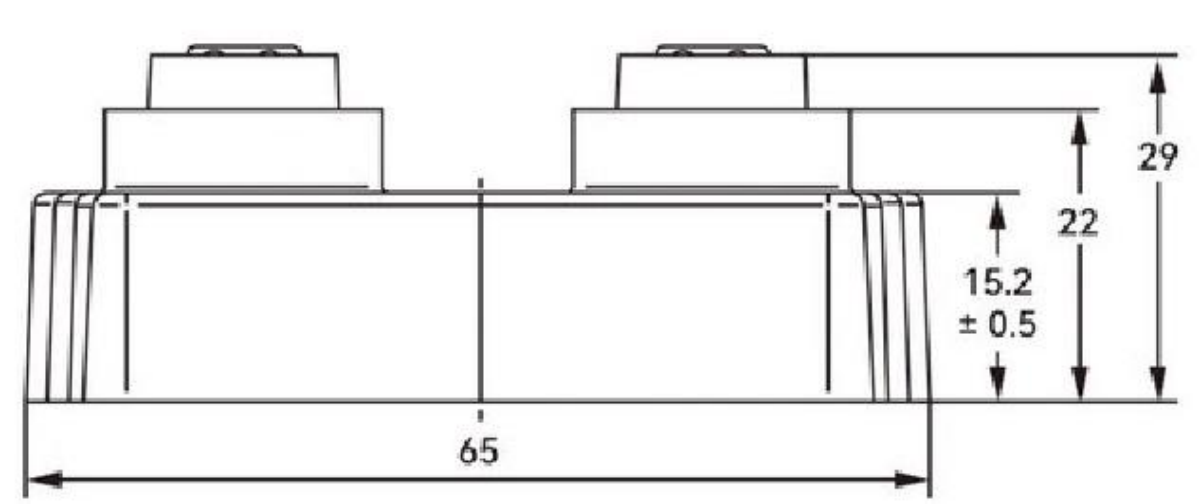
Shunt Current Measurement By using our website and services, you expressly agree to the placement of our performance, functionality and advertising cookies. Learn more